Measuring the flow rate of flare gas is challenging because a flare is not a pure gas, but a mixture of many different gases. In order to correctly measure the flow rate of the constituent gases, the composition of the flare must be known.
The Challenges of Measuring Flare Gas
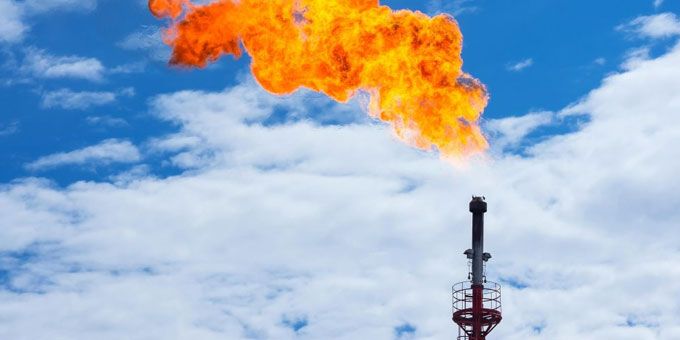
Scott Rouse, Product Line Director | Sierra Instruments
The associated gas generated from oil production has received a lot of attention recently. In many areas, the lack of gas collection infrastructure requires this gas to be flared off. Many jurisdictions now require the flow rate of gas to the flare to be monitored in order to reduce emissions and to allocate taxes, fines and other fees.
Measuring the flow rate of flare gas is challenging because a flare is not a pure gas, but a mixture of many different gases. In order to correctly measure the flow rate of the constituent gases, the composition of the flare must be known. This is typically determined by taking a sample (a cut) and processing it through a gas chromatograph (GC). This composition coupled with the total measured flow rate allows the flow rate of the individual component gases to be calculated.
Once the gas begins to flow from a well, operators need to account for this associated gas from day 1. This of course requires a flow meter calibrated to measure the flow rate of the flare gas. Virtually all current flow measurement technology requires a known composition for calibration. This presents a “chicken or egg” problem, since the composition may not be known at start-up and will change over time, thus rendering the flow meter inaccurate at best and inoperable at worst.
Achieving Flare Gas Measurement Accuracy Regardless of Changing Gas Composition
Recent innovations in immersible thermal flow meter technology provide a solution to this “what came first” problem. Sierra’s QuadraTherm flow meter can accurately measure the mass flow of gases over a very wide turn-down. Most importantly, users can change the meter’s calibration in the field to reflect the actual gas composition. This is made possible by an industry first algorithm called qMix, which uses the NIST RefProp database of gases to calculate the heat transfer properties of complex gas mixtures and thus maintains meter accuracy.
qMix Mathematical Model – How It Works*
QuadraTherm’s advanced mathematical model operates a microprocessor-based system that provides the foundation for making in-the-field compositional compensation. In a thermal mass flow meter, a velocity sensor measures the heat removed from a heated sensor by the flowing gas, while additional sensors measure other heat losses, such as those caused by natural convection, radiation, stem and end loss. The heat removed by the flowing gas is proportional to the mass flow. In operation, the four-temperature microprocessor-based system measures the resistance of each of four RTD sensors along with the current in the velocity sensor. The resistance values are converted to their four corresponding temperature values, and the current to the velocity sensor is converted to electrical power, or wattage. The four temperatures, the wattage, and the gas composition are the inputs to the system. The gas property algorithms calculate the updated properties of the gas (mass density, dynamic viscosity, thermal conductivity, and heat capacity). The system then computes the total mass flow rate in the pipe line – the desired output.
QuadraTherm meters can thus be stocked on the shelf, so that when a spare or new meter is needed, they can be installed, and the sample gas composition programmed in upon start-up of the well, thus ensuring day 1 flow measurement accuracy.
Download “New Developments in Thermal Dispersion Mass Flow Meters: In-The-Field Compensation for Changes in Natural Gas Composition” for more information on advances of QuadraTherm with qMix.
*Reference: Blog copy reprinted from Olin, J. G. 2014. New Developments in Thermal Dispersion Mass Flow Meters: In-The-Field Compensation for Changes in Natural Gas Composition. Presented at 2014 American Gas Association Operations Conference, Pittsburgh, PA, May 20-23, 2014.
The content & opinions in this article are the author’s and do not necessarily represent the views of AltEnergyMag
Comments (0)
This post does not have any comments. Be the first to leave a comment below.
Featured Product
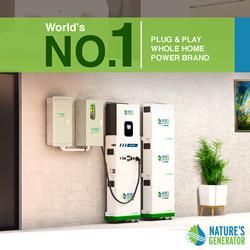