As the vehicle moves, a new area of the tire continually deforms and relaxes in a cyclic pattern whose frequency is dependent upon the speed of the vehicle. The piezoelectric bender elements would deform and relax with the tire. This deformation allows for the collection of
Len Calderone for | AltEnergyMag
Today’s electric vehicles use batteries to supply energy to make the vehicle move. The problem is that the batteries have limited power, which means that battery powered vehicles can only be used for short trips. However, hybrids include an internal combustion engine that uses conventional fuels, which recharge the batteries extending the vehicle’s range. This approach challenges the purpose of having an electrical vehicle, which would reduce environmental impact using renewable energy. There is still a need to generate more clean power that allows the maximum range of a vehicle to be extended with minimal environmental concerns.
To do this, a piezoelectric array is mounted in one or more tires of the vehicle. As the vehicle drives down the road, the tire is flexed during each revolution to distort the piezoelectric elements and generate electricity. An electric circuit delivers the energy to the electrical system of the vehicle.
There have been other attempts to do basically the same thing, such as the mounting of electrical generators on the axles of the vehicle to generate electricity during braking. Another example is found in attempts to extract energy from the shock absorbers of motor vehicles. Attempts have also been made to incorporate electrical generators in the wheel.
Piezoelectricity, also called the piezoelectric effect, is the ability of certain materials to generate an AC voltage when subjected to mechanical stress or vibration. The most common piezoelectric material is quartz.
The piezoelectric effect occurs when the charge balance within a material’s crystal matrix is disturbed. When there is no applied stress on the material, the positive and negative charges are evenly distributed so there is no potential difference. When the lattice is changed slightly, the charge imbalance creates a difference. This current is extremely small and would only cause a small electric shock.
A piezoelectric array is mounted inside a pneumatic tire of a motor vehicle and flexed or distorted during each revolution of the tire. Because of the inherent nature of piezoelectric devices, distortion creates an electron flow. The outputs of the piezoelectric devices are connected to an electric circuit to transfer the high voltage, low amperage electricity produced by the piezoelectric devices into low voltage, high amperage electricity that is compatible with the electrical system of motor vehicles.
Piezoelectric materials can convert mechanical energy to electrical energy, and vice versa. To accomplish this, piezoelectric units are bonded to the inner liners of tires. As the wheels rotate, the tires repeatedly distort and slacken as they interact with the road. This causes the piezoelectric units to produce a periodic voltage with a speed-dependent frequency. The energy that is generated can be used as auxiliary power to prolong the life of batteries.
Each piezoelectric vehicle tire is equipped with an array of highly bendable PZT (lead (Pb), zirconia (Zr), Titanate (Ti)) benders covering most of the inner surface. The output, due to deformation of tires, is an AC waveform, which has to be converted into a DC signal by a rectifier before it can be stored in a capacitor. Each row of benders, running across the width of tire is taken as one generator and is rectified separately with all PZT lines connected in parallel. At any given time of driving, only three or four rows— depending on the length of the arrangement of the contact patch—generate power.
The incorporation of sensors within the wheel removes the need to rely on a limited power source such as a battery thereby allowing an increase in usable sensor life.
A tire maintains its circular shape when not moving. Movement of the vehicle causes a section of the tire to conform to the shape of the road—it flattens out. The sidewall just above the contact area also undergoes deformation by bulging out. As the vehicle moves, a new area of the tire continually deforms and relaxes in a cyclic pattern whose frequency is dependent upon the speed of the vehicle. The piezoelectric bender elements would deform and relax with the tire. This deformation allows for the collection of energy.
To send energy to the battery, engineers could use a connection running from the tire to the hub and on to the battery. Or they could transfer energy with an induction current. Power is obtained from the tire/wheel system using an assembly that constantly maintains the electrical contact between the chassis and the wheel while letting the wheel spin freely. Such a setup allows the extraction of tire-generated power to run the onboard electronics.
The energy harvested by bonding piezo benders depends on three factors—tire surface area, rpm at 60 mph, and bender end-to-end deflection. These factors are a function of tire radius with a larger radius resulting in a larger surface area, lower rpm, and lower deflection. Different tire sizes will produce a different power output depending on the combination of these factors.
The future of advanced driver assistance systems will be contingent on the vehicle making all its decisions based on the assumption that the tires can withstand it all. And maybe they can, if the tires are factory produced, and haven’t worn out the tread. This calls for sensing construction far more advanced than that of a tire pressure monitoring system, bringing us into the scope of advanced tire intelligence. The sensors needed for such intelligence would require power.
These sensors would need some special characteristics, such as being able to operate on miniscule pulses of power, and the ability to be powered by the motion and pressure of the tires and the vehicle’s interaction with the road.
The amount of pressure that we are dealing with is only transitory, since the vehicle is a moving object. The piezoelectric energy harvesting will need to be done just under the tread. A crystalline layer sandwiched between two different tread layers would serve the purpose.
The batteries in an electric vehicle are self-charged as the car is in motion, due to the power generated by the tires. Therefore, only a one-time external charging is required. This is exactly what is needed when you're in the middle of nowhere and your car might not reach the next charging station.
For additional information:
-
https://pdfs.semanticscholar.org/1db1/7493e23dd1b120db2ba8b6656aa34ad648b8.pdf
-
http://www.ndt.net/events/NDTCanada2011/proceedings/papers/40_Makki_Rev1.pdf
The content & opinions in this article are the author’s and do not necessarily represent the views of AltEnergyMag
Comments (0)
This post does not have any comments. Be the first to leave a comment below.
Featured Product
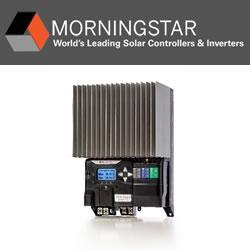