This technique is projected to reduce solar panel manufacturing costs by upwards of 60% compared to industry standards, while making them 25% more efficient, and resulting in a very cost-effective source of energy.
Using Particle Accelerator Technology to Manufacture Solar Cells
Contributed by | Rayton Solar
Rayton Solar is a California-based solar panel company that aims to develop the world’s most cost-effective source of energy. By bringing together essential particle accelerator technology and solar energy manufacturing, Rayton has created silicon cutting and handling techniques that can be leveraged to transform the way electricity is generated around the world.
How it Works
Have a look at their StartEngine Crowd Funding Page here.
The content & opinions in this article are the author’s and do not necessarily represent the views of AltEnergyMag
Comments (0)
This post does not have any comments. Be the first to leave a comment below.
Featured Product
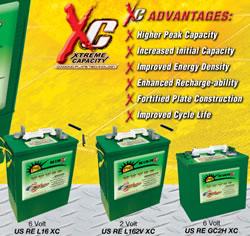