As PMG+FPC drive trains outperform DFIGs from both a full-cycle cost-efficiency and reliability perspective, the turbine manufacturing industry needs to revise some of its old assumptions and obsolete turbine technology choices to embrace the generator technology that leads to better AEP.
Panu Kurronen | The Switch
A mere decade after it was introduced in the wind industry, permanent magnet drive train technology has moved from the margin to the mainstream to become the go-to solution for modern wind turbines. Competing double-fed induction generator (DFIG) and converter solutions are losing steam. When analyzed either from the perspective of total life-cycle cost efficiency or from reliability, the PMG with a full-power converter (FPC) is by far the best technology, regardless of which key decision-making criteria is used.
The long-term advantage comes from the extra energy produced with the higher power curve efficiencies of PMG technology. Its great contribution to lowering the Levelized Cost of Energy (LCOE) explains why traditionally conservative OEMs have progressively come to incorporate this disruptive technology into their turbine design.
A full understanding of LCOE
The big challenge has been to get the industry to fully understand the advantages of advanced drive trains that lead to better performance and lower LCOE. Permanent magnet technology represents permanent performance through high reliability, overall efficiency and high-quality electricity.
There are still markets throughout the world where the initial investment decision-making criterion is price. These include emerging markets just getting into wind, for example. Still, we see a clear market for premium turbines that feature a higher upfront cost, but much better total life-cycle performance. PMG has been proven to provide the lowest LCOE.
In China, for example, the first phase of wind turbine technology development was mainly built based on licenses from Europe. Therefore, turbines based on induction generators were built originally. The first ones were based on a standard asynchronous machine and a soft starter. Later on, drive trains advanced to feature a DFIG and converter. Finally, along with the shift into the new millennium, came a shift in technology towards new solutions represented by PMGs and FPCs.
When The Switch entered China in 2004, there were no PMG-based turbines in production. Still, some open-minded companies had that technology on their drawing boards. Over the past ten years, we have witnessed the PMG revolution in China. In fact, all Chinese wind turbine manufacturers that have really been successful during the past ten years have selected PMG+FPC based drive trains in their turbines. They have been lucky to be able to leapfrog ahead to the most modern technology, since they were able to select their own turbine designs from scratch once the license phase was over.
The main reasons for the PMG+FPC drive train success today in all parts of the world are high reliability and availability, combined with the ease of handling existing and future grid connection requirements, such as low-voltage and high-voltage ride-through. Drive trains with FPC can also handle requirements for feeding reactive power. DFIG machines cannot reach the same level without an external power conditioning device.
One of the final obstacles to PMG popularity was when the development of rare earth material prices experienced considerable fluctuation a few years ago. This scared off many companies from moving faster into the use of PMG. Yet for approximately the past two years, the price of rare earth magnets has stabilized with the entry of new suppliers in various parts of the world. This has led to a healthy balance of supply and demand.
More energy, lower grid connection costs
It is sometimes claimed that PMG+FPC drive trains are more expensive than DFIG drive trains. However, when every investment and operational factor is taken into account, PMG+FPC drive trains work out to be a cheaper, more cost-effective option over the total life cycle of the turbine, despite slightly superior upfront costs.
Specifically, the lower grid connection costs of PMG+FPC equipped turbines represent a significant advantage over DFIG models. Since efficiency and grid compliance are the top demands when it comes to generator selection, it’s an important element to keep in mind. While partial converters may have improved somewhat in grid code compliance, full-power converters remain the preferable option. These factors, along with high annual energy production (AEP) and reliability, are very important from an investment point of view.
DFIG technology now complies with the grid codes by adding hardware and software with an extra cost. Although this simply answers the problem, it is more of a quick fix than a concrete solution. With fault ride-through and power factor capability, the DFIG converter becomes similar in size and cost to the full converter. A key benefit of PM drive train technology is the fact that it already includes features such as reactive power generation and low voltage ride-through (LVRT). These inherent benefits level the playing field when making comparisons with the cheaper upfront costs of DFIG drive trains, which also need additional VAR support to make a connection to the network.
Another long-term advantage also comes from the extra energy produced with the higher power curve efficiencies of PMG technology in low or medium wind conditions. The PMG’s maximized energy production is what gives significantly higher income and profitability. This is especially true when operating at partial power, where the highest number of operational hours of a wind turbine’s lifetime is spent.
PMG+FPC drive trains actually improve efficiency over the full operational range of the turbines. Although some claim that DFIGs are more efficient than PMGs at full load generation and in high, steady winds, the efficiency of the PMG+FPC drive train and the DFIG+partial converter are only similar when operating at 100% power. Yet, we know that this situation rarely occurs. Therefore, PMG drive trains have proven to be more efficient in general working conditions.
The fact that DFIG only needs a partial converter reduces the difference in total drive train efficiency between these two concepts – especially at nominal loads. At partial loads, however, there is a significant difference – and this is where a wind turbine operates most often with fluctuating wind speeds. This is why a PMG drive train results in higher AEP.
Design simplicity for superior reliability and serviceability
PMG designs also enhance reliability and serviceability, leading to lower O&M costs. It is important to bear in mind the required servicing and total reliability of the drive train. On this account, PMG designs have a comparatively low number of electrical faults and failures. The annual service costs of PMG technology can be up to 30% lower than the service costs for DFIGs. Moreover, generator losses are always lower with PMG than with DFIG, since there are no excitation losses.
One of the common misconceptions in the industry is that PMG+FPC solutions require lots of potentially unreliable electronics. This commonly admitted myth states that full-power converters are not very reliable because they rely greatly on power electronics, which would be more prone to faults than gearboxes. This is inaccurate. In reality, the amount of electronics used in PM drive trains is comparable to DFIG systems. More importantly, it is worth noting that there are no electronics used in the PMG generator itself, only in the converters.
Furthermore, when considering a multi-megawatt system, a DFIG solution most likely consists of only one converter for the rotor connection, while a full-power converter system can consist of several parallel power threads. As semiconductors do fail, it is better to have healthy power threads in operation despite a failure in one of them. This allows the turbine to run at limited partial power, rather than having the whole turbine at a standstill due to a failure in power electronics.
PMGs require the use of NdFeB magnets, which are sensitive to corrosion and heat. For this reason, some industry commentators claim that electrical losses could climb rapidly due to excessive heat. They also wrongly assume that there is a risk of reversed polarity or permanently losing magnetic field strength.
Such statements seem to ignore the fact that NdFeB magnets are always coated, which helps to protect them from corrosion very efficiently. Hermetic sealing is also applied when assembling the rotor, which also helps in this regard.
In addition, PMGs have high reliability and low maintenance costs due to better heat performance than the DFIG, as well as being able to function without slip rings or encoders.
Leading the world of wind power
It is clear that the old DFIG and other conventional designs will remain. But the majority of new designs in China and the rest of the world are based on field-proven PMG+FPC technology. And these are now leading the way – and the world of wind power.
As PMG+FPC drive trains outperform DFIGs from both a full-cycle cost-efficiency and reliability perspective, the turbine manufacturing industry needs to revise some of its old assumptions and obsolete turbine technology choices to embrace the generator technology that leads to better AEP.
About Panu Kurronen
Dr. Panu Kurronen is Product Manager, Permanent Magnet Generators, at The Switch in Lappeenranta, Finland. Prior to joining the company at its very start, Panu worked as a technical manager at Rototek Finland Oy, one of the three companies that initially merged to form The Switch in 2006. Panu graduated as a Doctor of Science (El. eng.) from Lappeenranta University of Technology in 2003. Over the years, he has worked as a researcher, laboratory manager and associate professor at Lappeenranta University of Technology. From 1995 to 2000, Panu worked as project manager at Kone Elevators. His focus has always been on the application of permanent magnet technology.
The content & opinions in this article are the author’s and do not necessarily represent the views of AltEnergyMag
Comments (0)
This post does not have any comments. Be the first to leave a comment below.
Featured Product
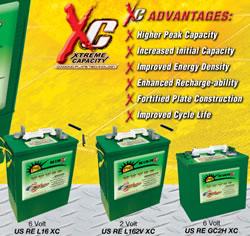