Ultracapacitors have other significant advantages compared to batteries such as high power density, high efficiency, long service life, predictable aging, wide operating temperature range and light weight.
Ultracapacitor Usage in Wind Turbine Pitch Control Systems
Stefan Werkstetter | Maxwell Technologies, Inc.
Modern applications in the growing renewable energy market have intensive requirements on both their components and operating strategy. As the costs for electricity generated by renewables such as wind and solar decrease and ultimately reach the electricity generation costs of conventional power plants [1], the demand for components with high reliability and high efficiency increases. Since 1999, Maxwell Technologies, Inc. (Maxwell) has consistently been providing short-term energy storage solutions for electric pitch control systems in wind turbines.
Introduction to Pitch Control Systems
General Overview
Today, pitch control systems in wind turbines are a standard component. The pitch control system is continuously adjusting the blade pitch in accordance to the operation strategy of the wind turbine. This ensures constant power output of the wind turbine.
Due to the ongoing trend of developing larger wind turbines with larger rotor diameters to achieve a higher power output, the entire system is exposed to additional effects of non- uniform wind fields where the wind speed at the highest point can vary from the wind speed at the lowest point. This results in an uneven force on the individual blades, the shaft, gearbox and the entire wind turbine structure. Pitch control systems can be used to compensate for this mechanical stress to extend service life of the wind turbine.
As an emergency function in the case of grid failure, an energy storage system provides enough energy to return the blades to a neutral position to ensure a safe shutdown. This functionality prevents severe damage or total loss of the wind turbine.
Pitch control systems are built either as electrical or hydraulic systems. Both versions have merit for different environmental conditions.
Hydraulic Pitch Control Systems
Approximately 35 to 40% of wind turbines in the field are equipped with a hydraulic pitch control system. These systems include hydraulic actuators to turn the blade, valves, an accumulator tank, and a hydraulic power unit with one or more pumps. The hydraulic power unit is installed in the nacelle, and the actuators and the accumulator tank are installed in the rotating hub.
A significant advantage of hydraulic systems is their relatively low complexity as no gears are required to pitch the blades. Also, the initial system cost is low.
A typical weakness of hydraulic systems is the high energy consumption due to the continuously running pump. Furthermore, the high pressure can lead to hairline cracks in the hydraulic components. The usage of hydraulic fluid requires maintenance efforts on a regular basis and holds the risk of oil leakage over time.
Nevertheless, hydraulic pitch control systems have proven their reliability in the field.
Electric Pitch Control Systems
Electric pitch control systems include electromechanical actuators to turn the blade, electrical controllers, a power supply unit, and an energy storage system. The power supply unit is installed in the nacelle, the actuators and the energy storage are installed in the rotating hub. A slip ring ensures power transfer from nacelle to hub.
The major advantage of these systems is the high efficiency. Depending on the energy storage solution, long maintenance intervals can be achieved. The ongoing operational costs are also lower due to lower maintenance requirements. Two types of energy storage systems have been utilized: battery based and ultracapacitor based.
Typical disadvantages of battery based electrical pitch control systems are the repetitive maintenance efforts for the battery itself and the higher number of components in battery monitoring which increases the complexity of the entire system. The associated maintenance costs with battery based electrical systems can be largely mitigated through the use of ultracapacitors.
Figure 1 Independent electromechanical pitch actuators
Battery Pitch Control Systems
About 35 to 45% of the wind turbines in the field are equipped with a battery electrical pitch control system.
Initial costs for battery-based pitch control systems and ultracapacitor-based systems are equal today. Battery based systems are likely to have a sophisticated charging and monitoring system to maximize life and provide battery safety. Batteries also have a narrow operating temperature range and are significantly stressed by harsh environmental conditions. Due to these reasons batteries are often replaced every 2 to 4 years [3].
Ultracapacitor Pitch Control Systems
Approximately 20 to 30% of the wind turbines in the field are equipped with an ultracapacitor electrical pitch control system.
Ultracapacitor-based pitch control systems have a lower total-cost-of-ownership than battery- based systems. The electrical system costs excluding the energy storage itself tend to be lower due to simpler charging and monitoring systems. Ultracapacitors charge faster compared to batteries, perform better under harsh environmental conditions and are projected to operate for up to 12 years in normal operating conditions [4], [5]. Moderate temperatures and an aligned operating voltage ensure long mean service life of ultracapacitors.
Ultracapacitor Technology Overview
As of the end of 2013, there are nearly 30,000 turbines worldwide equipped with 7 million Maxwell ultracapacitor cells with capacitance ranges from 350F to 3000F. Maxwell´s customer base includes 40% of the top-ten wind turbine manufacturers. Maxwell´s industry-leading product line has a variety of solutions from single ultracapacitor-cells to market-specific modules.
Ultracapacitors, Electric Double Layer Capacitors (EDLCs), and Supercapacitors are synonyms. An ultracapacitor is an electrical charge accumulator, having both extreme capacitor plate specific area and atomic scale charge separation distance. This results in very high capacitance. In addition, no chemical reactions occur during charge or discharge cycles.
Ultracapacitors store energy with a very high efficiency. This highly reliable energy storage buffers short term mismatches between the power demand and the power availability. Ultracapacitors can be operated in a wide operating temperature range, showing excellent low temperature performance. It is not uncommon for ultracapacitors to operate with an efficiency of 97% and higher.
The cycle life, depending on cell type, is between 500k to 1M charge/discharge cycles under normal operating conditions [4], [5]. This can result in a mean service life of up to 12 years. Maxwell has developed several ultracapacitor modules optimized for electric pitch control applications in cooperation with established wind turbine manufacturers. The modules include a passive balancing circuit to ensure all cells are charged to the same voltage level. To achieve higher system voltages, the modules can be connected in series.
Figure 2 typical Maxwell modules used in pitch control systems
Ultracapacitors vs. Batteries
Energy Storage Technology Overview
Today both batteries and ultracapacitors are used as energy storage in electric pitch control systems. Both technologies have their individual advantages and weaknesses. The following Ragone plot compares various energy storage/propulsion technologies as a function of energy density and power density. The diagonal lines define the time constant/”charge time”.
Figure 3 Ragone plot of various energy storage technologies [2]
Battery Properties
Batteries are known for high energy density, but generally have limited power density (charge/discharge rate). In addition, continued high rate cycling deleteriously affects both battery performance and lifetime. To maintain lower rate (and thus longer life), battery-based energy storage has to be oversized to accommodate peak power demand even if this demand occurs only for a few seconds. This leads to significant weight and cost addition to the system. Complex monitoring systems are required to determine SOC (state-of-charge) and SOH (state- of-health) on a regular base and to be certain to avoid overcharge and over temperature situations. Low temperature environments will demand even bigger battery energy storage systems to compensate the poor low-temperature performance of common electrochemical technologies. Battery lifetime is limited to a few years at best and is further decreased with continuous cycling and harsh environmental conditions. This requires periodic maintenance and battery replacement. Such maintenance can be even more problematic and costly if these systems are installed in offshore wind turbines. In winter or under stormy weather conditions maintenance cycles of offshore turbines can extend up to several months.
Ultracapacitor Properties
Ultracapacitors are a good choice for electric pitch control systems due to their operational properties, especially the high power density. An electric pitch control system has a low energy demand which can be easily fulfilled by ultracapacitors. The typical duration for a blade pitch order is approximately 30 seconds. Ultracapacitor based systems are smaller and lighter and they do not need to be oversized to accommodate high power cycling. Furthermore, ultracapacitors are known to be a green technology due to their high efficiency and the materials used during manufacture.
A wide operating temperature range (-40°C to +65°C), long lifetime and outstanding cycling stability ensure a maintenance-free operation for up to 12 years [4,5]. Compared to batteries, ultracapacitor based systems can also require less monitoring and less sophisticated management systems. Their aging is highly predictable.
Comparison of Battery and Ultracapacitor Properties
Figure 4 Comparison of batteries and ultracapacitors
Cost Considerations
Initial Cost
The portion of costs of a pitch control system compared to the entire system cost of a wind turbine is between 3 to 5%.
Currently battery based pitch control systems and ultracapacitor based pitch control systems can be designed at equal initial cost. Considering total cost of ownership, the balance shifts in favor of ultracapacitor based systems due to the long life and minimal maintenance. This is even more dramatic in cases where location of the wind turbine makes maintenance difficult.
Initial Design cost
Compared to battery based systems, ultracapacitor based systems require simpler monitoring and management systems. Also mechanical mounting and vibration damping of ultracapacitors is simpler than mounting for batteries. Due to the wide operating temperature range, no heating or cooling of the ultracapacitors is required. These circumstances lead to lower initial design-costs and hardware effort of ultracapacitor pitch control systems.
Maintenance Cost
Ultracapacitors have lower maintenance & replacement costs due to longer service life and minimal maintenance requirements. Wind farm owner and operators can increase turbine reliability and reduce battery related cost (incl. revenue loss) on average by $30,000 to $60,000 over 20 years, depending on the PPA (power purchase agreement) and turbine size (e.g. 1.5MW or 2.5MW).
Lost Opportunity Cost
Ultracapacitors have lower unplanned losses due to longer product life and better aging predictability under normal operating conditions [4]. This leads to less downtime even while reducing maintenance requirements.
Comparative Cash Flow
Currently battery based pitch control systems and ultracapacitor based pitch control systems can be designed at equal initial cost, so initial system cost can be set to 0 for a comparable cash flow overview.
Running Cost
Batteries are typically replaced after 4 years, ultracapacitors after 10 years [4,5] . Energy storage costs are nearly the same for batteries and ultracapacitors. The plot below shows the replacement cycle and the energy storage cost impact. This calculation does include energy storage cost without labor costs.
Figure 5 Running cost of energy storage replacement
Total Cost of Ownership
Considering a 20-year-period as typical wind turbine service life, the total energy storage cost due to periodical battery replacement is two and a half times the total cost of an equivalent ultracapacitor energy storage system.
This calculation does include energy storage cost without labor cost.
Figure 6 Total cost of ownership of energy storage replacement
Summary
Electromechanical pitch control systems provide substantial advantages over hydraulic pitch control systems in wind turbine systems. As a backup energy storage system, either ultracapacitors or batteries are used.
Compared to battery systems, ultracapacitor systems have a significant lower total cost of ownership at similar initial cost. If initially designed-in, ultracapacitor based systems can be comparable in cost to battery based systems.
Finally, ultracapacitors have other significant advantages compared to batteries such as high power density, high efficiency, long service life, predictable aging, wide operating temperature range and light weight.
[1] Kost, C., Schlegl, T. Studie Stromentstehungskostenerneuerbare Energien. Fraunhofer ISE, Freiburg,Germany. December 2010
[2] Adapted from US Defense Logistics Agency Report
[3] Dr Sherif El-Henaoui, “When the Wind blows – Pitch Control Systems Turn”, 2009 http://www.moog.com/literature/ICD/Moog_WindArticle_ENGLISH_1July09.pdf
[4] Results may vary. Additional terms and conditions, including the limited warranty, apply at the time of purchase. See the warranty details and datasheet for applicable operating and use requirements.
[5] Specifications available on Maxwell cell and module datasheets must not be exceeded to attain results noted.
Stefan Werkstetter
Stefan Werkstetter is a Senior Field Applications Engineer at Maxwell Technologies, Inc., the world's leading manufacturer of ultracapacitors. He is based in Maxwell’s office in Munich, Germany. Stefan is a state-certified electrical engineer with a focus on computer science. He has several years of experience in electrical systems pre-development, evaluation and testing. Prior to joining Maxwell, Stefan worked in the automotive industry for a German original equipment manufacturer and as a technician in telecommunication electronics.
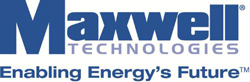
About Maxwell Technologies
Maxwell is a global leader in the development and manufacture of innovative, cost-effective energy storage and power delivery solutions.
Our ultracapacitor cells, multi-cell packs and modules provide safe and reliable power solutions for applications in consumer and industrial electronics, renewable energy, transportation and telecommunications.
Our CONDIS® high-voltage grading and coupling capacitors help to ensure the safety and reliability of electric utility infrastructure and other applications involving transport, distribution and measurement of high-voltage electrical energy.
Our radiation-mitigated microelectronic products include power modules, memory modules and single board computers that incorporate powerful commercial silicon for superior performance and high reliability in aerospace applications.
The content & opinions in this article are the author’s and do not necessarily represent the views of AltEnergyMag
Comments (0)
This post does not have any comments. Be the first to leave a comment below.
Featured Product
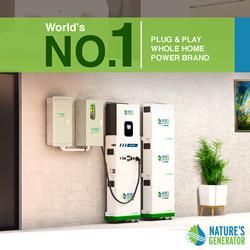