The roads constructed using this technology are more durable and economical than the conventional bitumen roads.
Creating Roads from Waste
Rajnish Ahuja, | Associate Fellow at Pahle India Foundation
Pune is a city in the state of Maharashtra, seventh largest metropolis in India and houses some of the well known manufacturing industries and automobile industries as well as the Government & Private sector Research Institutes, Information technology, Management and Training institutes. The city has a population of nearly 3.1 million with population density of 4451 per kilometer square. Most of the Indian cities have an informal waste management system that works in parallel with the municipal systems that are usually overburdened by other chores.
With no other option left, the residents in Pune were obliged to place their waste in roadside containers which are emptied daily. The problem with these containers is that the containers need to be maintained regularly or else they get corroded or are damaged and overflowing containers is a common complaint of residents within the vicinity of the containers. Also, plastic waste decays very slowly and hence a solution to reuse the same had to be found out apart from the recyclable plastics.
The Pune Cantonment board found a solution to the problem of disposing plastic by making use of a mixture of waste plastic and bitumen to relay a 250-metre stretch of the road connecting Lawrence road and Cross road within Pune Cantonment Board limits. The roads constructed using this technology are more durable and economical than the conventional bitumen roads. The combination of bitumen and waste plastic used for making the roads was 90:10 where the shredded plastic is obtained by chemically treating plastic waste generated from urban areas. The waste plastic includes a large amount of plastic bags and packing material. The technology has been cleared by the Central Pollution Control Board from the point of view of the pollution generated while the construction of road is on. The company who laid the stretch used 430 kg of shredded plastic for the 250 metre-long stretch. The technology was replicated to lay roads of length up to 1,500 kilometers in Maharashtra.
Source: http://indiacivic.com/savenature/jusco-plastic-road-future/
What is the Technology?
The waste plastic is heated within a temperature range of 100 - 160°C, which softens it and the plastic exhibits good binding properties. After that, the softened plastic is blended with bitumen that results into a mixture which is amenable for road laying.
The Process:
- The collected plastic waste with a maximum thickness of 60 microns is cleaned and dried and then shredded into small pieces, where the sizes generally range from 2.36 mm to 4.75 mm.
- The mixture is then heated to 165°C in a mini hot mix plant
- Shredded plastic is added to the hot mix and owing to the exposure to heat; it gets softened and gets coated over the surface of the aggregate.
- Hot Bitumen, which has been pre heated to a temperature of 160°C is added to the contents are mixed well and then the mixture is cooled to 110 - 120°C for laying the road.
The added sustainability to the roads is that the road strength is twice stronger than normal roads with a resistance towards water stagnation (no formation of potholes), avoidance of plastic burning and less consumption of bitumen.
The content & opinions in this article are the author’s and do not necessarily represent the views of AltEnergyMag
Comments (0)
This post does not have any comments. Be the first to leave a comment below.
Featured Product
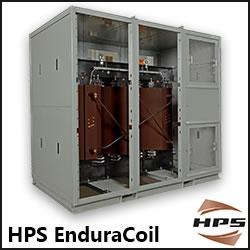