An automated approach takes the guesswork out of siting. Software-generated algorithms automatically search the solution space, quickly and efficiently providing planners with a near optimal solution that can statistically be guaranteed.
Solving Wind Farm Siting
Yogesh Khandelwal, Joe Jordan and Dan Liggett | geoAMPS
The same sophisticated computer process that has been used to engineer the structure of a space satellite antenna and formulate financial trading strategies through multiple scenarios is being utilized by the wind industry to site wind farms and turbines.
Multi-objective adaptive heuristic algorithms are computer instructions that automatically search project criteria and siting issues in an efficient manner to provide wind farm planners a set of near optimal solutions.
Siting a wind farm and individual turbines within the farm is critical to the project’s success. Siting, however, is more complex than buying or leasing any available property and placing turbines randomly. There is the availability of regular and considerable wind current to consider. Other issues include environmental and wildlife impacts, land ownership, existing infrastructure, proximity to utility lines, population density, regional land use, topography, and the costs of clearing land and developing access roads.
Wind farm developers have found new Web-based software to be useful in navigating these complexities. geoAMPS, a technology company located in the Columbus, Ohio, area, has developed a software product called altAMPS that automates much of the information essential to making siting decisions.
Also known as genetic algorithms, multi-objective adaptive heuristic algorithms are computer instructions that adapt Charles Darwin’s evolutionary model. The process interchanges design elements in hundreds of thousands of different combinations. Only the best-performing combinations are permitted to survive.
Wind turbines work best on high, exposed locations. Hilltops are ideal, as long as there is a flat area and suitable ground for the tower. The vicinity should be clear of obstacles which could interfere with the wind current or operation of the turbines.
Certain sites can be removed from consideration quickly based on federal, state and local government regulations and restrictions; land use and geological constraints; and adverse impacts on the environment or wildlife.
For those locations that pass those tests and are regarded as the best feasible sites, still more data is required, such as availability of wind, land ownership, proximity to utility lines, topography, infrastructure, population density and site preparation costs.
An important preliminary procedure in siting is placement of one or more meteorological (met) towers. With attached anemometers and wind vanes, these towers measure wind speed and direction specific to the site under consideration. At least one year of collected met data is recommended.
Sorting through the complexities of siting a wind farm, one or more met towers, and multiple wind turbines is a difficult process. Meanwhile, substantial investment is on the line. Developers resort to various means to arrive at what they hope will be the best siting decisions.
Some companies still work from pencil, paper and calculator. This process is unlikely to result in optimal siting. As more factors are taken into account – such as wind speed, costs and regulations – the metrics and rules grow exponentially. This traditional approach quickly becomes unsustainable.
Other companies use a semi-manual process. Through computer-assisted design, wind farm developers simulate possible locations through a geographical information system (GIS) interface. They gain instant feedback with each minute change to the spatial orientation of the turbines. This feedback includes values of desired calculated metrics. It red-flags certain locations when any siting rules defined at the outset are violated.
There are, however, countless possible placements of turbines within a proposed wind farm, a fact which can make this approach, although superior to the manual process, too time-consuming and inefficient. Even after such a long, arduous process, wind farm developers may not have arrived at the best siting options.
An automated approach takes the guesswork out of siting. Software-generated algorithms automatically search the solution space, quickly and efficiently providing planners with a near optimal solution that can statistically be guaranteed.
Planners define areas of interest and project objectives and rank factors on a weighted scale of importance. Met tower and GIS data is included. GIS mapping data can be applied to information from local agencies and third-party providers. Planners learn quickly about zoning or government restrictions. They obtain information about environmental or wildlife impacts, topography, weather patterns, infrastructure, population density and placement of utilities. Title information on individual parcels, which previously took days to research at the county courthouse, is available instantaneously and can greatly speed the right of way negotiation process.
The software performs a directed search and determines several siting solutions, numbering them in the order of best fit.
Siting wind farms and individual wind turbines on those facilities can be a complex process. As the image shows, Automatic Optimization provides wind companies with the quickest and best possible siting solution.
(Image produced by geoAMPS)
This automated approach can eliminate nearly all the time spent developing wind farm layouts and transform it into evaluating optimized layout and choosing the one that best suits project needs. If underlying factors change, re-evaluating the options is a simple change requiring minimal re-work.
Multi-objective adaptive heuristic algorithms have been used across other industries to solve the same type of complex problems wind farm planners face in siting decisions. Financial organizations have used them to formulate trading strategies. The method even has been used to arrange a constellation of satellites in space, and to engineer design of a space satellite antenna. It reduces development time and financial risk, while simultaneously increasing efficiency and maximizing profit.
A wind farm project represents a significant investment of time and resources. The capabilities of automated siting optimization can help wind companies maximize the return on that investment.
As President and Chief Executive Officer of geoAMPS, Yogesh Khandelwal is an engineer with a diverse background in technology across various industries. With more than 15 years of experience in database configuration and implementation, he helps organizations implement standardized processes, bringing efficiency and optimization within project and asset management. He completed master’s degrees in civil engineering from The University of Toledo and The Ohio State University.
Joe Jordan is Product Development Manager at geoAMPS. He leads development and maintenance of the Web-based geographic information system (GIS) viewer and detached application. He completed a bachelor’s degree in engineering from Clemson University and a master’s degree in financial mathematics from The University of Dayton.
Dan Liggett is Communications and Public Relations Manager of geoAMPS. He has an extensive background in the newspaper industry and in public relations for higher education and public transportation. He holds a bachelor’s degree in journalism from Ohio University.
For more information call 614-389-4871 or visit www.geoamps.com.
The content & opinions in this article are the author’s and do not necessarily represent the views of AltEnergyMag
Comments (0)
This post does not have any comments. Be the first to leave a comment below.
Featured Product
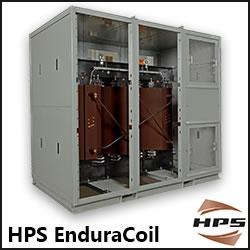