Coatings are the first preventative measure for all of these assets. Since most are being deployed in desert areas or mountainous areas or along the coasts, or sometimes in the water, choosing the right coating is imperative to achieve design life.
Corrosion Control for Wind and Solar Equipment
Rick Grant | Russell Corrosion Consultants, Inc.
What does RCC do?
RCC is a specialty corrosion engineering firm. We focus on analyzing and mitigating our clients corrosion issues through state of the art corrosion engineering practices. These solutions come in a variety of forms, some can be as simple as applying the right coatings, others more complex in that they require layered solutions, i.e., coatings and cathodic protection designs.
How are companies engaging RCC for corrosion control issues? What are you investigating?
Clients are engaging us all across industry. Particular to the alternative energy segment, clients are asking us to assist them in a variety of ways. For instance, our alternative energy clients would like to know how corrosive the environments are in regards to where they are deploying their assets to, once that is known how that will affect their assets in terms of achieving their desired design life, and finally what solutions can they implement to achieve their design life should corrosion be an issue. In addition many of these clients are asking us to do a design review of their proposed assets and to assist them in choosing the right materials and coatings to better withstand the hardships of their proposed deployment areas.
What are the biggest concerns from the solar and wind manufactures?
The biggest concerns from a corrosion perspective is will my asset be affected by corrosion and if so how? And what does this affect have on my design life?
What can RCC recommend to achieve intended design life?
There are many factors that affect corrosion rates, to name a couple prevalent ones in this industry they are: material selection and corrosivity of the environment. RCC needs to review all the design specifications which will tell us if there are any dissimilar metal connections that may cause a corrosion cell, to determine the types of materials being used and how they interact with the type of environment they are being deployed to, what types of protective coatings (if any) are being proposed and is it the right kind for the right environment (it’s not one stop shop), and finally we would perform an environment site assessment to determine how corrosive the area of deployment is. Once we know all these factors we can recommend solutions to our clients to achieve their design life.
How do coatings and cathodic protection fit in to your recommendations?
Coatings are the first preventative measure for all of these assets. Since most are being deployed in desert areas or mountainous areas or along the coasts, or sometimes in the water, choosing the right coating is imperative to achieve design life. Some deployment, depending on conditions will require coatings and a cathodic protection solution, whereby we purposely set up a corrosion cell but corrode our targeted material (i.e., anode) thereby protecting the asset from corroding.
What is the additional cost incurred to protect offshore wind equipment (as a percentage of project cost)?
I don’t have firm costs I can share. Since all of our projects involve different sizes, materials and deployments the costs vary accordingly. However, to engage RCC to perform corrosion analysis and design mitigating solutions is a very small percentage of overall project costs as a whole.
Are you seeing growth in the offshore wind industry based on inquiries for corrosion control advice?
We are seeing growth across all of the alternative energy sector. Clients are realizing they need expert help in this matter, and that the cost of not doing a proper corrosion control analysis is far greater should their assets fail. Our alternative energy practice is the fastest growing practice area at RCC. We performed over 15 distinct projects just last year alone across the world and were actively working on another 8 just in Q1 2013.
What parts of the world are most involved in offshore wind projects?
The world is a large place, were seeing activity in progressive countries that take alternative energy seriously.
Russell Corrosion Consultants, Inc. has made the Inc. Magazine's 500/5000 list for 2011 and 2012, for the fastest growing companies in the US.
The content & opinions in this article are the author’s and do not necessarily represent the views of AltEnergyMag
Comments (0)
This post does not have any comments. Be the first to leave a comment below.
Featured Product
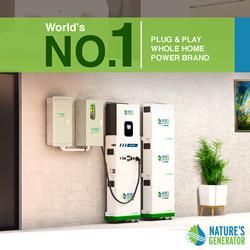