Light weight, strength and corrosion resistance represent three of the benefits. "Aluminum profiles can be made as structurally strong as needed for most applications,"
Aluminum Continues KnowledgeSurge in Cost-driven Solar
Kevin Widlic | Hydro Aluminum Extrusion Americas
ISA Corporation guarantees its new rooftop solar solutions for 15 years. The long-span mounting systems are all-aluminum, with stainless steel connection hardware. Aluminum was its best material alternative, something ISA did not know until the design began taking shape.
ISA uses aluminum in the major beam structure and in its clamping systems.
“We need the light weight because of the load allowance for the roof and because it makes it easier to get the systems up on high-rise buildings,” says company president Tony Zante. “Corrosion resistance is another factor.
“When we were designing the new system, our aluminum supplier – Hydro – showed how the flexibility of the metal could help us optimize the metal and the system design. I don’t think we were fully aware of the possibilities until then.”
Maximizing the material
ISA presented its new systems at Intersolar North America 2012, which gathered some 900 exhibitors. Many of the manaufacturers of PV structures who were present at the show utilize aluminum – and primarily extruded aluminum – in their systems. The group included Mounting Systems, one of the largest and most experienced manufacturers of solar mounting systems in Europe.
Mounting Systems established production in California in 2011. “The trend in our industry today is probably related more to costs than anything else,” says chief executive Kasim Ersoy.
“We use a lot of aluminum in our products. Aluminum is not a cheap material, but we know how to maximize the characteristics of the material, for instance in design, and this makes aluminum competitive to other materials with regard to cost.”
Competitive total cost
ISA and Mounting Systems are adapting, and benefiting, their material decisions well-grounded. The consulting firm Deloitte recently completed a quantitative analysis on the total cost of ownership (TCO), comparing aluminum with steel as the material choice for structural building projects, which could include photovoltaic mounting systems.
The TCO approach considers four cost categories:
- Acquisition
- Installation
- Maintenance and operations
- Disposition
In developing the basis for its research, Deloitte noted that “costly project decisions tend to rely on existing practices, rather than exploring new opportunities for long-term cost savings. Evaluation criteria often do not take into account a time frame that represents the project’s actual lifespan. This hinders the use of alternative processes and/or material choices that could realize significant cost benefits.”
Further on, the firm explains that while steel remains the material of choice in structures, including PV systems, when it comes to replacing steel, aluminum “provides the same benefits at a lower total cost of ownership.”
Light weight, strength and corrosion resistance represent three of the benefits. “Aluminum profiles can be made as structurally strong as needed for most applications,” writes Deloitte, which adds that “the case for aluminum becomes even more apparent when the project is located in a highly corrosive environment.”
The firm concludes that “over its entire lifespan, an aluminum structure may prove to be the best option in terms of installation, maintenance, operation and disposition costs.”
Better for mounting structures
IBIS Associates focuses its consulting work on competitive position assessments of traditional and advanced materials and manufacturing technologies. Its research on the total effect of light-weighting vehicle components, for example, is highly regarded within the automotive industry.
IBIS performed an analysis that is similar to the one done by Deloitte, but which zeroed in the costs related to the fabrication, assembly, shipping and installation of PV mounting structures. It compared extruded aluminum with galvanized steel – and its conclusions were equally clear.
“When taking into account the total cost of materials,” the firm writes, “aluminum is a more economical alternative to steel in PV mounting structures, across all market segments. In addition to this demonstrated initial cost advantage, you can expect structures built with aluminum extrusions to have a lower Total Cost of Ownership, primarily as the result of lower ongoing maintenance costs and substantially higher residual value.”
Other advantages to using extrusions for PV structures, compared to steel, include:
- Low density and high strength-to-weight ratio
- Low tooling costs and unlimited design flexibility to optimize performance and reduce fabrication steps
- High corrosion resistance for superior durability, even in extreme environments
- Ease of recycling and high scrap value
Getting the word out
Hydro Aluminium is delivering fabricated aluminum solutions to an increasing number of companies in each segment of the solar industry. So are many of its competitors in the aluminum business.
At the same time, the aluminum companies often find themselves running into the same challenge – tradition – when approaching potential customers about new projects.
“We made knowledge about aluminum the theme of our booth at Intersolar, and we will do the same at SPI in Orlando,” says Allan Bennett, who is responsible for Hydro’s solar business in North America. “We want to show companies that they have a viable material alternative that is cost-competitive and sustainable, as green as the industry they are supplying.”
The content & opinions in this article are the author’s and do not necessarily represent the views of AltEnergyMag
Comments (0)
This post does not have any comments. Be the first to leave a comment below.
Featured Product
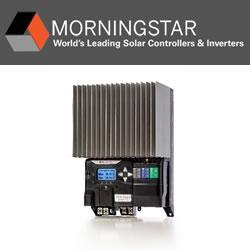