Here are 16 of the potential failures or damages that can occur on a solar farm and how they could impact operations if not addressed in a timely manner.
Anything Can Go Wrong on a Solar Farm
Maureen McHale for | ESA Renewables
When it comes to solar power plants, a critical consideration to achieving maximum power output is the ongoing operation and maintenance (O&M) following the commissioning of the system. Although solar installations are highly reliable and designed to run with minimal manpower, efficiency will be lost and energy generation decreased if not maintained properly.
Solar equipment can be kept in service for decades with regular and proper attention to all major and ancillary features; however, many asset managers may not have a handle on what is really needed in the day-to-day operations of a power plant. Undetected failures and small issues impact the overall operations of the system, which leads to lost revenues and lower energy generation compounding with each undetected, unmanaged issue.
Protect Your Investment
Having an O&M company that can service utility scale and commercial photovoltaic systems takes much of the stress out of the equation. Not only can this type of company perform the necessary scheduled maintenance, they also will manage anomaly alerts, make system repairs, evaluate network voltage and frequency, monitor and report on energy production, and other critical factors related to the solar array.
An O&M agreement provides a working plan to cover repairs, protect warranties, and perform preventive maintenance. To ensure a facility is operating at optimum efficiency and not losing money, an O&M provider will generally install a monitoring system to not only keep a close watch on all of the arrays working components to achieve maximum performance, but also to analyze and report on energy production, trend costs, produce quick budgets on site and more.
Utilizing state-of-the art technology and highly experienced solar energy engineering staff, an O&M company has the ability to track all of the indicators and parameters to optimize performance and to carry out the required maintenance of each solar farm.
16 Potential O&M Issues
Here are 16 of the potential failures or damages that can occur on a solar farm and how they could impact operations if not addressed in a timely manner.
- Perimeter Fence Damage. Damage caused to the perimeter fence can immediately have a negative effect on facility operations. Whether the damage was due to vandals, a storm or even an animal, this is an item that needs immediate attention. Not only can people be injured due to the high voltage produced by the system, but the expensive equipment is at risk if intruders enter the area with intent to destroy or steal items. Regular inspection and quick response to this is crucial for all solar farms.
- Ground Erosion. A naturally occurring process in nature, soil and ground erosion are caused by water and wind. Expected as a gradual occurrence and planned for at a certain periodic rate, sudden erosion can have a deleterious effect on a PV plant. Loss of topsoil can lead to reshaping of the ground and the creation of channels, holes and slopes in earth. This could cause racking to shift affecting the ability of panels to generate the energy. It could also lead to flooding and destruction of equipment. Proper and frequent site monitoring will alert asset managers to anything out of the ordinary happening that could put operations at risk.
- Transformer Leakage. Routine maintenance that certifies that transformers are in good condition every year helps avoid transformer leakage. A transformer leak can cause land contamination and other safety risks. Knowing if a leak is present and planning for maintenance to repair or replace it can be key in keeping energy generation at a maximum. There several ways to carry out preventive maintenance in transformers; however, monitoring transformer oil temperature, pressure and level to prevent a transformer from leaking in the first place is the best way to avoid down time issues. To prevent fatal errors, a parameter range is set and automatic alarms can be issued to check on site before the problem scales.
- Various Inverter Damage. Taking the low voltage, high current signals from PV panels and converting into the voltage compatible with the utility grid, inverters are core components of grid-connected systems. Monitoring of inverters is of high importance, since changes to voltage and frequency may occur that affect performance as well as the safety of those in proximity. Inverter damage may lead to the complete failure of the PV plant or partial string outages as a result of defective inverters. Inverter failures are responsible for roughly 80% of PV system downtime. Clearly a response to any inverter damage must be taken quickly.
- Broken Conduit. A broken conduit poses danger of shock as well as chaos on the operating system as charges are uncontained. When the construction of a site is finished and the plant goes into operation, earth movements may happen as the ground stabilizes. These movements can cause broken conduit and other issues with cables. Measuring isolation on cables ensures underground runs are damage free. This is important because broken conduit can cause a cable to break or damage the insulation which can cause a fire and personal hazards.
- Combiner Box Damage. With the ability to simplify wiring, combiner boxes combine inputs from multiple strings of solar panels into one output circuit. Normally 4 to 12 strings are connected to a combiner box. If damaged, they pose a safety risk as well as a major decrease in productivity.
- Vegetation Overgrowth. Vegetation can transform from a benign nuisance in to a major issue very quickly. In addition to attracting animals that then cause their own brand of destruction, vegetation can shade cells, interfere with wiring and affect structural integrity.
- Cell Browning/Discoloring. In addition to providing power, UV radiation will lead to aging in panel cells, seen as browning and discoloration. This degradation in the film leads to impaired output and productivity.
- Panel Shading. When designing a PV plant, it is critical that trees and other obstructions are cleared. PV cell electrical output is very sensitive to shade. If shaded, cells do not add to the power produced by the panel, but they absorb it. A shaded cell has a much greater reverse voltage compared to the forward voltage of an illuminated one, it can absorb the power of many cells in the string and the output will fall drastically. Removal of any trees or structures causing shading will help optimize power output.
- Shorted Cell. A shorted cell can impact productivity if not addressed in a timely manner. Production defects in semiconducting material often go undetected before PV cells are put into solar panel assemblies. Identifying these defects through testing via infrared imaging has been used for more than a decade. This efficient, cost-effective test and measurement methods for characterizing a cell’s performance and its electronic structure help ensure maximum energy production.
- Natural Damage. A hail storm or hurricane can wreak havoc on a solar power plant. Damaged panels, or wind torn racking and other equipment can severely decrease output or completely put a system out of commission. Keeping a pulse on the severe weather and inspecting the equipment following a storm is necessary for the overall health of the solar farm.
- Vandalism Damage. Vandals pose a major threat to any PV facility. Whether they are stealing or destroying wiring, panels or other equipment, system damage can occur. A solar farm in North Carolina had golf ball damage by a neighbor who decided to use the array as the 18th hole. Detecting this damage through the use of solar monitoring equipment minimized outages and losses.
- Defective Tracker. An exceptional tool to enhance early morning and late afternoon performance, trackers can increase total power produced by about 20-25% for a single axis tracker and about 30% or more for a dual axis tracker. Defective trackers can contribute significantly to lowered performance output and should be serviced as soon as detected.
- Racking Erosion. Eroding structures can be a nightmare for a PV facility. Once the structural integrity is degraded, risks to proper water and wind flow within the facility are elevated which can gravely impact the functioning of the facility. As racking moves, panels are moved from their optimal positioning and energy generation suffers.
- Unclean Panels. Dust, snow, pollen, leaf fragments, and even bird droppings – all can absorb sunlight on the surface of a panel, reducing the light that reaches the cells. Clean surfaces result in increased output performance over the lifespan of the equipment. Routine cleaning should be a part of all O&M plans.
- Animal Nuisance. No matter whether an animal burrows under a perimeter fence, jumps over it or goes right through it - animals need to be kept out of a solar farm. Once inside the perimeter, they seem to have a way of finding wires to chew and unknowingly destroy equipment.
Having an O&M agreement for a solar farm is a must. Paired with a monitoring system , many of these issues can be prevented and energy production maximized. If you are an asset manager in need of an exceptional O&M company, contact ESA Renewables.
An Ideal Partner
Customized operations and maintenance packages offer customers a cost effective and efficient way to keep their renewable energy systems at optimal performance levels. For solar farm owners that do not have the staff on site to maintain the installation, ESA Renewables, LLC (ESA), a turnkey solar solutions provider, offers O&M contracts customized to each solar farms needs.
ESA proudly provides financing, engineering, procurement and construction (EPC), and O&M services to customers throughout the world. Additionally, ESA has developed its own proprietary renewable energy monitoring system complete with a newly developed cost project and control module and is one of the first O&M providers to offer a solar power production guarantee. With a local presence and the extensive reach of ESA's O&M personnel for onsite repair services, customers are ensured that outages and faults are quickly resolved to provide optimal system performance.
Backed by years of experience gained from their testing facility, in the engineering of innovative products, inverter monitoring, and site expertise, ESA has not only installed multi-megawatts of power, but also currently provides ongoing O&M services for solar installations for customers worldwide.
For more information about ESA Renewables O&M services, their Power Productions Agreements or their proprietary Monitoring System, please visit their website, http://esarenewables.com or call 407-268-6455.
About the Author
Maureen McHale is a Marketing Consultant located in Central Florida. Maureen has extensive internet marketing experience and has successfully developed, launched and promoted products and services for companies in industries ranging from high-tech, to travel, funeral and more for over fifteen years. For more information about Maureen's capabilities, please visit her website, http://hiremaureen.com or call 352-406-2011.
The content & opinions in this article are the author’s and do not necessarily represent the views of AltEnergyMag
Comments (0)
This post does not have any comments. Be the first to leave a comment below.
Featured Product
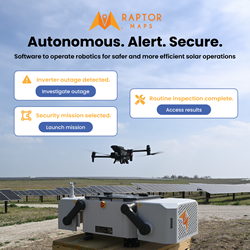