The S.P.M. Mill operators initially tried using Oscillator and Vortex technology flow meters. They found that these flow technologies contain moving parts or orifices and were unable to measure flows accurately at the low flow rate demanded by this digester application.
Advanced Biogas Thermal Mass Flow Meter Boosts Methane Recovery System Operation
Steven Craig | Fluid Components International LLC
Introduction
S.P.M. Feed Company Limited is based in Pakto, Pak Tho Ratchaburi, Thailand and manages over 100,000 head of swine. The company is an active participant in the organic biomass fermentation and recovery industry. S.P.M. generates power from biogas produced by the organic industrial waste from the livestock (Fig 1). Additionally, the company derives benefits from trading the excess fuel for clean energy development credits: Clean Development Mechanism (CDM).
On-Farm Methane Recovery
Decomposing livestock waste on feed mill farms and other agricultural operations is a major source of methane-rich biogas. The operators can easily harvest it as fuel gas. Rather than emit greenhouse gases into the environment, modern farm operations invest in a digester system to recover gases and reduce emissions. Recovered gases are used to fuel electrical generators to power the facility. Additionally, excess power is sold to the local electric power grid. CDM and certified emission reduction (CER) programs offer additional incentives to implement these methane recovery systems.
The Problem
Biogas recovery systems have basic requirements. They must accurately measure the flow rate of methane and other mixed gases in order to ensure effective and efficient operation of the digester process. Also, effective operation of the gas turbine equipment that uses the biogas from the digester process to produce electric power depends on accurate flow rate measurement of methane. Reliable flow rate measurement is also required in order to provide tangible evidence of saved emissions (CER) and to receive credits and incentives from government agencies (CDM).
Consistent with most agricultural operations, the S.P.M. Feed Mill operators collect manure from the livestock. They then digest it using anerobic conditions in specially constructed reactor tanks that produce methane. The company needed a biogas-specific gas flow measurement technology in order to accurately measure volumetric gas flows and report the amounts to a CDM broker. Biogas measurement applications present several challenges in selecting the proper flow meter:
- Low flow sensitivity due to the low flow vapor recovery from the digester process
- Temperature compensation for correct readings in varying temperatures
- Calibration for mixed gas composition of CH4 + CO2 + trace gases
- Wet and dirty gas
- Potentially flammable or explosive gas installation environment
- Easy, low cost installation and low maintenance
Biogas is wet and dirty with particulates that quickly foul and clog with most flow meter sensing technologies. The dirty wet gas also will foul meters that are designed with moving parts and orifices. The S.P.M. Mill operators initially tried using Oscillator and Vortex technology flow meters. They found that these flow technologies contain moving parts or orifices and were unable to measure flows accurately at the low flow rate demanded by this digester application.
S.P.M. also found that they experienced repeated flow meter failure due to the wet and dirty gas. Clogged parts from the wet and dirty biogas environment caused the Oscillator and Vortex flow meters to fail. Using these flow meters, S.P.M. also encountered inaccurate measurement results.
In one example of inaccurate results, the lowest flow rate measured by these technologies was 100 NCMH. With the flow rate being so low, the Vortex flow meter could not measure the gas accurately enough to support the output of electric power. Also, the workers found they had to shut down the Oscillator and Vortex flow meters several times each month for manual cleaning. These ongoing maintenance requirements interfered with farm operations and productivity.
The Solution
Based on its flow technology research, S.P.M. specified the ST51 Biogas Flow Meter, a thermal flow meter from Fluid Components International (FCI). The ST51 Biogas Flow Meter uses constant power technology to measure wet and dirty air and gases. The ST51 Biogas Flow Meter (Fig 2) is specifically designed as a low cost solution to solve the unique challenges to flow metering in digester process generated methane.
The ST51 delivers methane gas flow with accuracy to a reading of ±1% over a broad flow range (from 0.08 to 122 MPS) and repeatability of ±0.5 percent of reading. The flow element is available for use in line sizes from 2 to 24 inches (51 to 610 mm) diameters. It operates over a wide turndown range of 100:1, which is essential due to the variable gas flows in wastewater treatment. It operates at temperatures from -18 to 121°C and withstands pressures up to 500 psig [34 bar (g)].
The thermal dispersion mass flow measurement technology of the ST51 Flow Meter positions two thermowell protected platinum 1000 ohm RTD temperature sensors into the process stream. One RTD is heated while the other senses the actual process temperature. The temperature differential between these two sensors is measured and is directly proportional to the mass flow rate of the fluid (Fig 3). FCI’s thermal mass flow sensor design utilizes a constant power measuring technique, which provides stable flow sensing. This technology provides better accuracy and repeatability in moist biogas measurement applications.
The key benefits of the ST51 Flow Meter that caused the S.P.M. team to select the device were the biogas flow meter’s ability to operate continuously with high measurement accuracy and repeatability in a rugged biogas plant environment with virtually no maintenance (Fig 4). The ST51 Biogas Flow Meter features a no-moving parts thermal dispersion mass flow sensor design that is highly resistant to clogging. The ST51’s resistance to clogging means limited to no downtime required for maintenance and improved productivity. The device operates over a wide flow range with wide turndowns making it sensitive to the low-flow variable nature of biogas production applications.
Additionally, the ST51 is protected by an explosion-proof transmitter package that is suitable for combustible biogas environments and meets safety requirements. The transmitter is housed in an aluminum enclosure that is NEMA 4X approved and meets IP67 requirements for water and dust ingress protection. Input power for the ST51 can be selected as either 18 to 36 Vdc or 85 to 265 Vac.
Here is a high-level list of the key criteria for flow meter selection in a methane recovery application:
- Accurate and calibrated for specific biogas composition
- Mass or volumetric flow measurement
- Low flow sensitivity, as low as 0.08 m/s
- Wide ranging, 100:1 turndown
- Non-clogging, no moving parts for low maintenance
- No added pressure drop
- Approved for safe installation in explosive gas environment – system agency approvals for Division 1 [Zone 1, II2 GD Ex d IIC]
Results
S.P.M. realized two key benefits after installing the ST51 Flow Meter. They were able to generate power continuously, and reduce operating expenses due to lower installation and maintenance costs. They no longer need to interrupt the process to clean the flow meter on a monthly basis. They also have eliminated the fouling and clogging issues because the ST51 Flow Meter has no moving parts.
Table 1 displays the S.P.M. plant’s digester gas process specifications, flow, temperature and pressure after the installation of the ST51 Biogas Flow Meter.
Media: Biogas-4 components. Mole (Volume) Percentage.
Methane 65.000% Carbon Dioxide 34.500%
Hydrogen Sulfide 0.250% Oxygen 0.250%
Accuracy: 1.00% rdg. + 0.50% of full scale.
Repeatability: 0.50% rdg.
|
Normal |
Minimum |
Maximum |
Units |
Flow |
40 |
7 |
500 |
NCMH |
Temperature |
30 |
25 |
45 |
Deg C |
Pressure |
0.1 |
0.05 |
0.16 |
Bar (g) |
Standard Conditions: 1.01325 Bar(abs) and 0 deg C |
The content & opinions in this article are the author’s and do not necessarily represent the views of AltEnergyMag
Comments (0)
This post does not have any comments. Be the first to leave a comment below.
Featured Product
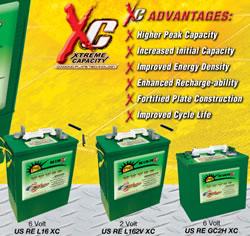