Our local manufacturing operations will allow Suntech to meet the growing demands of customers throughout the Americas, including our dealer network with more than 400 partners. One advantage is that all modules produced at the facility are compliant for procurement in American Recovery and Reinvestment Act (ARRA) projects. Also, in the long term, regional manufacturing will help to minimize our exposure to rising oil and transportation costs.
Steven Chan, President | Suntech America
2. What do you see as some of the advantages to having manufacturing in the US?
10. Does the plant now or in the future perform research into new solar technologies?
The content & opinions in this article are the author’s and do not necessarily represent the views of AltEnergyMag
Comments (0)
This post does not have any comments. Be the first to leave a comment below.
Featured Product
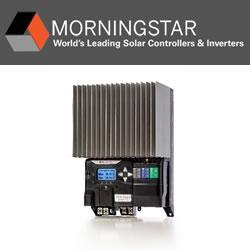