We got the opportunity to interview the three leading teams in the EcoCAR Challenge namely Mississippi State University, Virginia Tech and Pennsylvania State University. These are the future leaders in the alternative energy transportation industry and it shows in their enthusiasm.
Team Reps from Mississippi State University, Virginia Tech and Pennsylvania State University.
I got a chance to interview some of the leading student teams in the EcoCAR Challenge competiion so I jumped at the opportunity. These are the future leaders of the industry and I think they represented themselves very well here. We're at the end of Year 2 of the competition so stay tuned to see how this plays out next year. Good luck to all the teams.
1. Firstly, please give us a short summary of the main features of your vehicle.
Our vehicle is an Extended-range Electric Vehicle (E-REV), similar to the upcoming Chevy Volt. It uses a 21.3 kWh battery pack made of modules donated by A123 Systems to provide a 60-mile all-electric range. Once the battery is depleted, a 1.3L turbodiesel engine (which runs on biodiesel) then cranks up and turns a generator, which maintains the batteries at a relatively constant state of charge while the vehicle continues on. To recharge the batteries, just plug the vehicle into any standard 110- or 240V outlet. Charging can take up to 10 hours. The net result of all this is a 118 mpg gasoline equivalent, and throughout the course of a day's driving, most Americans won't use any liquid fuel at all.
2. What were the initial goals that you set out for your design team to accomplish?
We have a very detailed set of goals called Vehicle Technical Specifications (VTS) which we established before we began to design the vehicle. They include factors relating to fuel economy, emissions, performance, and consumer acceptability. Some of our notable goals include 107 miles per gallon gasoline equivalent (mpgge) and a 40-mile all electric range, both of which we exceeded.
3. How did you decide which configuration to build for the competition?
We established a design matrix and set of weighting criteria which evaluated vehicle architectures (configurations) for a range of over 50 variables. We then considered almost every configuration allowed within the EcoCAR rules and plugged them into our design matrix. This required months of computer modeling and number crunching. In the end, the diesel E-REV came out on top as the optimal design.
4. What was the vehicle you started with and what were the main changes you had to make to it?
The vehicle that we started out with was a conventional gasoline-powered 5-passenger crossover SUV donated by General Motors. It ran fine; we then proceeded to take out everything that already worked. The entire stock powertrain came out to make room for our plug-in hybrid powertrain. We have also made additions to add some creature comforts to the car, including upgrades to the gauge cluster and vehicle infotainment system.
5. How was the design process carried out? Describe the size and setup of your team(s).
Our team is divided into six groups: Mechanical, Powertrain, Electrical, Controls, Emissions, and Outreach. Each group has a group leader who is in charge of that group and reports to the team leader. Once a week, the team leader and group leaders meet to discuss what needs to get done that week (based on a project plan that extends through the end of the competition.) Then, the entire team meets (early in the semester, up to 80 students) and group leaders disseminate tasks to their individual groups. Work is typically done on the car at night, after classes. For the last three months of EcoCAR: Year 2, there was someone working on the vehicle nearly 24 hours a day.
6. How did you acquire the components needed to build the car?
Most of our components were donated by competition sponsors, such as General Motors, dSpace, Mathworks, A123, and Freescale.
7. Where did you go for guidance during the construction phase of the competition?
Each EcoCAR team has a mentor assigned to them from GM. We are very fortunate to have Bill Beggs, a GM engineer, as our mentor and liaison with GM. He has a wealth of knowledge on almost every part of the car, and if he doesn't know the answer, he knows who to ask.
8. Did your team have all the skills necessary to build the car?
The competition is truly similar to the auto industry in that it requires a broad range of skill sets. Fortunately Mississippi State University has strong programs in the disciplines required, and we've been able to recruit students who have all the right skills. It's amazing to look back over the past year and see how everyone took care of their job, how the team worked together, and how the car came together. Our team is also very fortunate that we are headquartered out of one of the country's premier automotive research centers, the Center for Advanced Vehicular Systems (CAVS). The equipment, tools, computing power, and knowledge base here make building a top-notch complex hybrid vehicle (in a few months!) possible.
9. Please outline a few of the main difficulties you ran into and how you overcame them.
The most challenging part of our year was component packaging; literally, fitting everything into the car. One of our VTS which we really stuck to was maintaining stock cargo capacity of the vehicle while adding a large, plug-in battery pack. It would have been easy to just stick the battery where your groceries are supposed to go and call it a day. Our students, however, worked out a way to package the entire battery underneath the existing rear cargo cover and not sacrifice any cargo capacity. We were the only team which was able to do this.
Another challenge was controlling the engine so that it automatically starts when the battery charge gets low. This involved lots of on-the-fly engineering by our controls team, but they were up to the task. At competition, the engine start-stop strategy worked perfectly.
10. Where did your car excel and where did it fail to meet expectations during the competition?
Our vehicle did really well in the fuel economy and emissions events, winning each one. This was particularly exciting because back during the architecture selection phase, we selected these criteria as the ones to place the most emphasis on. We also did well in vehicle performance events by winning the acceleration and autocross awards. Even so, our acceleration time did not meet our VTS. That means that this year we will have to address and correct this.
11. What would you do differently if you could start again from scratch?
Well, it's hard to find complaints from this year's competition. I think that last year (where we finished third) there were some things that we could have done differently in our presentations. To be honest, the idea of starting from scratch is so daunting that I can't even imagine it!
12. What's next for your car and the competition?
We still have many, many things to work out this summer and the upcoming academic year. We have to improve our ride quality and our 0-60 acceleration time. Reducing weight on the vehicle will be a big priority during the upcoming year. As far as what is immediately next, after the media attention and event requests die down from winning Year 2, we have to put together a recruiting push to bring in fresh blood for next year. There is always a lot of turnover on a student team of this nature. That's good, because it means that we're taking our graduates and putting them in jobs!
13. How do you think the future of Eco-friendly vehicle design will unfold and how will the public be engaged in the process?
This is a really exciting time to be in the auto industry because I feel like the machine that people will call "car" for the next 80 years is being designed right now. In the early 20th century, internal combustion engine (ICE) powered gas and diesel vehicles were battling steam and electric powered vehicles to become mainstream. Once the ICE demonstrated its advantages and developed an established infrastructure, people drove gas-powered cars for 100 years and never looked back. Now it has become apparent that something has to change. Whether the technology of the future is range-extended hybrids, or battery electric vehicles, or hydrogen fuel cells, it won't be decided by which one ekes out a higher efficiency than the others. It will be decided by which one the public accepts and which one establishes an infrastructure first. It's not about which technology is better, it's about which technology is better at the right time.
1. Firstly, please give us a short summary of the main features of your vehicle.
Our plug-in hybrid vehicle has a large battery pack, which has enough energy to electrically propel the car for 40 miles. The battery supplies power to an electric motor mounted on the rear axle. The battery can be recharged in 5 hours from a 240V outlet. After about 40 miles of driving, the battery charge will be depleted and therefore a flex-fuel 4-cylinder engine, mounted on the front axle through an automatic transmission, will turn on to provide propulsion. The vehicle can achieve about 80% reduction in petroleum energy use over normal drive cycles. It also maintains 5 passenger seating, a touchscreen user interface/radio and all of the safety features of a normal vehicle.
2. What were the initial goals that you set out for your design team to accomplish?
We had to have a running vehicle by a March 1st inspection deadline. The deadline got pushed back, but the team had to have all of the designed components integrated into the vehicle by that time. The vehicle was also supposed to be running and driving by that time. Designing a subframe to hold the rear electric motor was one of the early goals in the fall semester. It would have to be built and integrated early in the spring semester.
3. How did you decide which configuration to build for the competition?
The year 1 team decided on our “split-parallel” architecture based on the competition rules, fuels and architectures available. The team believed that an extended-range electric vehicle supported by a flex-fuel engine would be a conservative and robust design that would excel in petroleum energy reduction as well as performance.
4. What was the vehicle you started with and what were the main changes you had to make to it?
All teams were donated a small crossover SUV from GM. The main mechanical changes included integrating two electric motors and the large battery pack, along with all of the mounting structures and electronics necessary for the components to function in the vehicle. The second electric motor is considerably smaller, and acts as a belted alternator/starter which is mounted directly to the engine. This allows us to do engine idle-stop and quickly and quietly restart the engine when the vehicle is ready to drive off.
5. How was the design process carried out? Describe the size and setup of your team(s).
The team is composed of 24 mechanical engineering seniors and two graduate team leaders. The team is split into Mechanical/Electrical/Controls and each subteam is given the necessary tasks for the car for the year. Each significant change made to the vehicle goes through a design review with the two team leaders and faculty advisor before it is approved. Verification and validation takes place after the design is implemented, to ensure that it functions as intended.
6. How did you acquire the components needed to build the car?
Our electric motors had been purchased in the past and used in previous competition vehicles. Our inverters were purchased for us by a local company for use in the competition. The battery pack was donated by A123 Systems, one of the competition sponsors. Significant metal fabrication material was provided by our go-to fabricator, Tri-Fab Inc. out of Pennsylvania.
7. Where did you go for guidance during the construction phase of the competition?
Our advisor has considerable experience in the competitions and offered useful insights. We also consulted industry experts, such as Tri-Fab, for mechanical design recommendations.
8. Did your team have all the skills necessary to build the car?
We had a very diverse team this year, ranging from computer whizzes to full on mechanics and fabricators. Each member brought his or her own unique set of skills to the car, but all of them had the fundamental engineering theory as taught by Virginia Tech, which was crucial in designing successful components. Several team members had to learn the proper signal and handshaking protocols of Controller Area Network (CAN) communication, a standard in the automotive industry.
9. Please outline a few of the main difficulties you ran into and how you overcame them.
The electric rear motor would not fit in the stock vehicle subframe, so we had to come up with a new design. The design, along with any other designs involving structural integrity of the vehicle, was submitted to the competition organizers for approval. This “waiver” process ensures that all vehicles comply with the rules and are safe.
Another issue we had was electromagnetic interference (EMI) getting on to signal lines (Controller Area Network lines (CAN), specifically) and causing interference. In order to fix this, we shielded all of our three-phase lines for the electric motors as well as installed a “Y-capacitor” (basically an EMI filter) on the high voltage DC wires. These actions significantly reduced the amount of noise that we saw.
Our vehicle did not have a fully functioning electric vehicle mode due to a faulting motor inverter. The inverter would shut off above 45mph, and the electric traction motor would become unusable. To get around this and still provide a somewhat functional vehicle, the control strategy was programmed to immediately turn the engine on and enter our charge-sustaining hybrid mode in the case of an inverter fault. This behavior was seen at competition, and enabled the vehicle to continue driving even though the electric motor had faulted.
10. Where did your car excel and where did it fail to meet expectations during the competition?
As mentioned above, it failed to meet the full electric vehicle expectation, which ended up lowering our utility factor-weighted fuel economy. However, it excelled in consumer acceptability due in part to excellent component integration, clean fit and finish, and a team-designed touchscreen user interface. The vehicle also had the best braking performance of any vehicle, and put up the best 0-60mph acceleration time of any vehicle.
11. What would you do differently if you could start again from scratch?
We would research more thoroughly into the motor inverter that we selected, in order to ensure that it can operate at all vehicle speeds.
12. What's next for your car and the competition?
The car will continue on for Year 3 of the competition. Year 3 involves refining the vehicle in order to present it in May 2011 at competition as a 99% ready vehicle. The vehicle control strategy will be fine-tuned, and integrated components will be redesigned for better fit and finish. There will also be a considerable effort to lightweight the vehicle.
13. How do you think the future of Eco-friendly vehicle design will unfold and how will the public be engaged in the process?
To some degree, the vehicles that become available will have to be based on customer demand. There has been a strong demand for hybrids the past few years, as well as issues with energy security and petroleum use. This seems to have sparked a revival of electrification of vehicle powertrains, as there are a large number of PHEV, HEV and EV designs that are coming to market soon (Volt, Leaf, iMIEV, Focus, etc.).
1. Firstly, please give us a short summary of the main features of your vehicle.
Our vehicle is an Extended-Range Electric Vehicle (EREV) based off the classic series architecture. In our vehicle, all power to the wheels is provided by a 160 horse-power electric drive motor. The primary source of electric energy is a 330V Li-ion battery pack donated by A123 Systems located in the rear of the vehicle. Once the battery is depleted, an Auxiliary Power Unit (APU), consisting of a 90hp diesel engine connected to a 75kW electric generator, provides additional electrical energy to power the drive motor.
The drive motor Penn State utilizes in the vehicle is the same one found in GM’s Fuel Cell Equinox fleet as part of Project Driveway. With this motor and our A123 battery pack, our vehicle is capable of driving over 30 miles on electrical power alone. The APU starts the engine only after the battery has been depleted and maintains the depleted charge level of the battery. If a driver does not travel more than 30 miles in a day, they would never need to use a drop of fuel. The batteries can also be fully recharged from a 240V wall outlet in 4 hours or a 112V outlet in 9 hours.
2. What were the initial goals that you set out for your design team to accomplish?
The initial goal that the team set out for in the design phase was to make the most efficient vehicle as possible, while at the same time still maintaining consumer acceptability. We also designed for the ease of manufacturability and integration. An overall goal of the team itself is to educate its members about the design process of hybrid vehicles and have a better understanding of vehicle hardware and integration.
3. How did you decide which configuration to build for the competition?
The team chose the EREV-series architecture for many different reasons. One of the main reasons we chose this architecture was that it allowed us to take advantages of technological advancements since the last competition.
Powerful advancements in energy storage systems allow for more efficient use of grid based electric energy. It also made it possible for us to integrate a high power density Li-ion battery in our vehicle that could provide 30 miles of all electric driving. With new battery technology, plug in charging has become far more viable, and our vehicle is capable of charging from a standard household outlet.
Advancements in electric motor capabilities have also made a series architecture more viable. With more efficient and more powerful motors, electric vehicles can meet consumer expectations for vehicle drivability and performance when compared to traditional gasoline powered vehicles.
The technology was also a new challenge for the team to overcome as a whole. Many of the past vehicles the team has worked on were parallel hybrids, and the series architecture was an exciting new prospect.
4. What was the vehicle you started with and what were the main changes you had to make to it?
The vehicle we started with was a stock 2009 General Motors Donated Vehicle based on a crossover architecture. It had a two-mode transmission and a 3.6 liter V6 that ran on standard gasoline. The stock components were replaced with a 160hp GM electric drive motor, a 75 kW electric generator and a 1.3 liter turbo-diesel engine that runs on B20 biodiesel. The stock battery pack was also removed and replaced with a custom Lithium Iron-Phosphate battery pack. This involved fabricating entirely new mounts for each of the components.
5. How was the design process carried out? Describe the size and setup of your team(s).
For the competition, teams closely followed General Motor’s Vehicle Development Process (VDP), which served as the basis for the organization of competition years. Year-1 of the competition was based on modeling and simulation work. We made a list of specifications for our vehicle to meet and requirements for each of the individual components and sub-systems. The team then looked to source the components through sponsors and OEMs. After component selection, the team worked to model and package the components in CAD and used dynamic simulations such as Argonne National Laboratory’s Powertrain System Analysis Toolkit (PSAT) and Hardware-in-the-Loop (HIL) to verify our designs.
In Year-2 we worked to integrate the components following the designs and specifications from Year-1. After integrating components we tested the subsystems to verify our control algorithm and validate that components functioned as planned and anticipated.
6. How did you acquire the components needed to build the car?
The majority of the components were donated by competition sponsors. This Electric Traction System (the drive motor), 1.3L turbo-diesel engine, $10,000 worth of additional General Motors parts, and the actual vehicle platform itself were donated by GM. The battery modules contained within the battery pack, as well as the battery control module were donated by A123 battery systems. Vehicle controllers were donated by MotoHawk Control Systems, a division of Woodward. dSpace provided Hardware-in-the-Loop testing bench and technical support. Various other components of the vehicle that were not donated were sourced by students and then acquired using funds provided by the DEP, The Pennsylvania State University College of Engineering, and the Department of Mechanical and Nuclear Engineering at The Pennsylvania State University. The team also received a high level of support from the Larson Transportation Institute as they are providing all the lab space and facilities needed to develop such a highly technical vehicle.
7. Where did you go for guidance during the construction phase of the competition?
Competition sponsors and organizers were a great source of information to the teams. Each team also has a GM Mentor assigned to them to help with technical aspects and guide them along the Vehicle Development Process. Our GM mentor, Paul Shoytush, was instrumental in our progress as a team and was a huge help during the competition. We also have faculty advisors that have been very helpful and provided great guidance.
8. Did your team have all the skills necessary to build the car?
At the beginning of the year, not everybody on the team had the skills necessary to complete the task, but by the end, those who worked on the vehicle had extensive knowledge that allowed the team to build the vehicle. This was due in part to the knowledge and general know-how of our outstanding faculty advisor, technical advisors, and our General Motors Mentor, Paul Shoytush. The biggest challenge for most engineers was overcoming the crossover from reading out of a textbook and doing problems to actually doing hands on work and turning wrenches.
9. Please outline a few of the main difficulties you ran into and how you overcame them.
We had difficulties getting our diesel engine to run when we first received it. We did some trouble shooting on our end and looked into how we had implemented similar engines in the past. We also received a lot of support from GM and our GM mentor Paul Shoytush. Once we had the proper hardware and software installed we were able to get our engine running and integrate it into our vehicle.
Procuring components and working around lead times was always a challenge. In order to meet some deadlines, we outsourced a few of the more complicated and system critical components to local machine shops. This included a mount for our motor and the bellhousing on our engine which protects the engine-generator coupling and flywheel.
10. Where did your car excel and where did it fail to meet expectations during the competition?
Our vehicle excelled in the areas of ride and drive quality. We actually placed first in the drive quality event. This event judged cars on how smooth and comfortable the car drove. We were also runners up for Lowest Well to Wheel Greenhouse Gases, Lowest Tailpipe Emissions, and Lowest Fuel Consumption. Our team was also one of three teams to finish all of the dynamic events.
11. What would you do differently if you could start again from scratch?
The integration of our mechanical subsystems took longer than anticipated and led to some difficulties at competition. If we were to go back and do it all over, we would definitely look to have these systems integrated sooner so we would have more time to test and validate our components.
12. What's next for your car and the competition?
In Year 3 the team will be working to refine the control algorithm and optimize the components that were installed during Year 2. One of the main goals in Year 3 will be refining our emissions equipment. Another goal of Year 3 will be to ensure consumer acceptability of the vehicle. This includes everything from a paint job, seating, 12V-ports, to even cup holders and spots for spare change.
The Year 3 competition itself will be located at the General Motors Milford Proving Grounds in Milford, Michigan. The same 16 teams will be competing, but all with refined vehicles.
13. How do you think the future of Eco-friendly vehicle design will unfold and how will the public be engaged in the process?
There won’t be a single technology that dominates the auto-market as gasoline has. You’re starting to see more parallel and power assist hybrids on the road today and as the technologies mature, you’re going to see more series vehicles like the Chevy Volt, fuel cells like the Chevy Equinox in Project Driveway, and fully electric vehicles. The public will get to vote on these technologies with their hard earned cash at the dealer, just as they vote in every capitalist market.
The content & opinions in this article are the author’s and do not necessarily represent the views of AltEnergyMag
Comments (0)
This post does not have any comments. Be the first to leave a comment below.
Featured Product
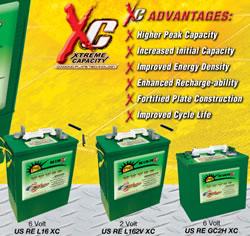