If you are a building owner that is considering a solar panel installation, there are several questions you should ask before signing any contracts. What is the best mounting method for installation on my rooftop? Do I need a new warranty to protect myself from any damage? Which type of system will give me the best ROI? Do I work with my old roofing company or do I need to find a structural engineer?
What Building Owners Need to Know Before Going Solar
Jen Lynch | Shorey Public Relations
With the Ontario Power Authority (OPA) giving the go ahead to begin hundreds of rooftop solar installations, building owners need to know their installation options, and not just focus on the financial perks associated with the new FIT. I wish I could relate this to opportunities offered here in New York, but there’s no comparison to the progress occurring across the border in Canada. Building owners and PV installers here may not offer the same financial incentives as their Canadian counterparts, but consumers that may one day invest in solar and install an array on their rooftop should be aware of the different technologies and installation options available.
Structurally Attached vs. Ballasted
There are several ways to integrate a solar array on a flat commercial rooftop. I am only going to discuss structurally attached and ballasted systems, but there is also a hybrid system that is a combination of both.
A ballasted system has panels that are not tied into the infrastructure of the building; they actually rest on top of the rooftop membrane. This system is the least expensive to install, but has several drawbacks:
- High potential of long term roof damage as a result of excessive weight combined with temperature changes causing the roof membrane to become brittle and crack
- Panels are required to be mounted at a lower angle, typically 0 to 20 degrees, to avoid any sail effect from even moderate wind, although there are a small number that can range higher
- Roof maintenance and replacement is more difficult
- Installation does not require any rooftop penetrations, but requires pre- and post- inspection and most ballasted systems only have a warranty for 10 years (the average lifetime of a standard commercial rooftop is 20 years)
- The system is less accommodating for low profile obstructions and roof pitch changes
- May require additional design around potential problem areas involving drainage, or the roof’s ability to shed water, snow or debris
- May require larger setbacks and labor to work placement around existing equipment
A ballasted system uses rubber boots or even cinder blocks to weigh down the racking on top of the roof membrane and must be completely removed in the event the landlord wants to replace or re-tar the roof. It’s also very important to determine the age of your roof before any installation, whether it be with a ballasted or structurally attached system. Older roofs have a higher likelihood of requiring replacement or repairs that can be very costly to the building owner, so it's important to keep that in mind.
The other mounting technique is to structurally attach the rack to the infrastructure of the building. While this method costs more upfront for the initial installation, it provides the following benefits:
- Results in the least amount of dead load to the building rooftop (dead load = PV array and equipment, live loads = wind, precipitation, dust/soil etc.)
- Increased options for panel angle, varying from 5-45 degrees (Since the system is tied into the support structure, you can generally increase the angle and approach optimum efficiency, without worry of sail effect from moderate wind)
- Enables you to have a level solar array regardless of roof drainage features, bumps, valleys, exhaust fans, vents, curbs or uneven areas that would prevent a ballasted rack
- Lower cost for racking components
- Covers the largest rooftop area
To my knowledge, Atlantic Wind & Solar Inc. (Ticker: AWSL) is the only company in the about-to-boom Ontario solar market that is offering 30 percent higher efficiency systems in this type of mounting system. This company caught my attention because of its unique combination of structurally attached arrays with an advanced high-yield converter/inverter technology (CIT).
Before I understood how a structurally attached rack was installed, I’ll be honest that I was skeptical about it… which made me realize that others most likely shared that feeling. I mean, who wants a number of holes drilled into their roof? After conducting further research however, I found that commercial rooftops already have holes cut into them for drainage and ventilation systems. And many commercial rooftops already have heavy air conditioning systems permanently tied into the building's structure, much in the same way AWSL’s solar systems are designed to be installed.
If you’re in Ontario or an area that receives a lot of winter weather, you may also want to look into the amount of efficiency lost when heavy snow covers the panels. With a structurally tied system set at a greater angle, common sense tell us that the snow will more easily slide off and not have as great an impact on efficiency. Even though we’re heading into the warmer months annual snowfall is certainly an important factor to consider.
Structurally Attached System + CIT = Best ROI
One thing the solar industry can always depend on is its critics, arguing that systems cost too much or the ROI isn’t high enough or the payback period is too long, and that’s just the beginning. So while ballasted systems are less expensive to install, their racking components cost more than a structurally tied system, but that system costs more in installation. Given these factors how do we resolve this problem?
Perhaps the reason why most integrators are not tying into the structure is that the extra cost of installation seems to hurt the initial ROI. I may agree in the case of using a conventional inverter, but with the extra CIT output that AWSL offers, I believe the ROI becomes high enough to make the investment feasible.
AWSL recently announced they will be acquiring 60 percent of the CIT manufacturer, AIM Global Energy, whose inverters achieve 30 percent higher system efficiency than industry norms. AIM’s new inverters are designed to turn on earlier in the morning and turn off later in the day, in order to capture more energy during a 24-hour cycle. An Ontario integrator, OzzSolar uses Satcon’s PowerGate Plus inverters that have been the inverter of choice in most solar installations to date in Ontario. Although they have a large share of the market and offer a variety of system installations, their inverter technology is no match for the advanced converter/inverter technology (CIT).
Considering that Ontario does not have optimal sunlight, it is even MORE important to be using the most efficient inverter in your solar system. I plan on doing more thorough research into this high-yield CIT, but what I know so far is that this advanced technology enables the inverter to turn on at just 120 VDC. Conventional inverters turn on at 320 VDC, and even with the addition of an external DC booster, can only reach a starting voltage at 190 VDC. This technology is clearly superior to any other in the market and I won’t be surprised if you start hearing more about Atlantic Wind & Solar and AIM Global Energy soon.
Roofing Contractor vs. Structural Engineer
I also found that companies that provide many types of systems but specialize in attached racks, like Atlantic Wind & Solar, use a structural engineering company to install the solar system instead of relying on a roofing contractor. These engineers design the system with the same sealing process that is used for typical exhaust vents or safety anchors. This process ensures that the solar system is seamlessly integrated into the structure and no future damage occurs. You also have to be aware that altering any design or layout of the panels after installation can void your warranty with the rooftop contractor. Pardon my skepticism again, but roofing companies also stand a lot to gain by approving these heavy load ballasted systems and coming back for repairs if roof becomes damaged.
The International Code Council (ICC) provides more specific details regarding the regulations and processes related to rooftop installation in the International Green Building Code (IGBC).
The content & opinions in this article are the author’s and do not necessarily represent the views of AltEnergyMag
Comments (0)
This post does not have any comments. Be the first to leave a comment below.
Featured Product
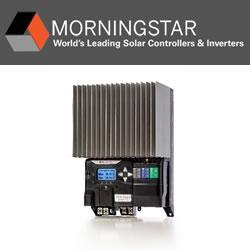