The challenges from agricultural requirements to produce food and energy can only be met if we use all options available for increasing productivity and safeguarding harvests. Innovative crop protection products and plant biotechnology provide solutions to reduce the energy consumption in agriculture while conserving natural resources and contributing to mitigate the effect of climate change.
Salman Zafar - Renewable Energy Advisor
Introduction
The term ‘Biofuel’ refers to liquid or gaseous fuels for the transport sector that are predominantly produced from biomass. A variety of fuels can be produced from biomass resources including liquid fuels, such as ethanol, methanol, biodiesel, Fischer-Tropsch diesel, and gaseous fuels, such as hydrogen and methane.
The first-generation liquid biofuels are made from sugar, starch, vegetable oil, or animal fats using conventional technology. The basic feedstocks for the production of first-generation biofuels come from agriculture and food processing. The second generation technologies use a wider range of biomass resources – agriculture, forestry and waste materials. Third-generation biofuels may include production of bio-based hydrogen for use in fuel cell vehicles, e.g. Algae fuel, also called oilgae.
Globally, liquid biofuels are most commonly used to power vehicles, heat homes, and for cooking. Biofuel industries are expanding in Europe, Asia and the Americas. Biofuels are generally considered as offering many priorities, including sustainability, reduction of greenhouse gas emissions, regional development, social structure and agriculture, and security of supply.
The biomass resource base is composed of a wide variety of forestry and agricultural resources, industrial processing residues, and municipal solid and urban wood residues. The forest resources include residues produced during the harvesting of forest products, fuelwood extracted from forestlands, residues generated at primary forest product processing mills, and forest resources that could become available through initiatives to reduce fire hazards and improve forest health.
The agricultural resources include grains used for biofuels production, animal manures and residues, and crop residues derived primarily from corn and small grains (e.g., wheat straw). A variety of regionally significant crops, such as cotton, sugarcane, rice, and fruit and nut orchards can also be a source of crop residues. Municipal and urban wood residues are widely available and include a variety of materials — yard and tree trimmings, land-clearing wood residues, wooden pallets, packaging materials, and construction and demolition debris.
Other advanced biofuel feedstocks include non-plant sources such as fats, manure, and the organic material found in urban waste. In addition, algae production has great promise because algae generate higher energy yields and require much less space to grow than conventional feedstocks. Algae also would not compete with food uses and could be grown with minimal inputs using a variety of methods.
Biofuel Feedstock Constraints
First-generation biofuels (produced primarily from food crops such as grains, sugar beet and oil seeds) are limited in their ability to achieve targets for oil-product substitution, climate change mitigation, and economic growth. Their sustainable production is under review, as is the possibility of creating undue competition for land and water used for food and fibre production.
The cumulative impacts of these concerns have increased the interest in developing biofuels produced from non-food biomass. Feedstocks from ligno-cellulosic materials include cereal straw, bagasse, forest residues, and purpose-grown energy crops such as vegetative grasses and short rotation forests. These second-generation biofuels could avoid many of the concerns facing first-generation biofuels and potentially offer greater cost reduction potential in the longer term.
Forest Resources
Primary
- Logging residues from conventional harvest operations and residues from forest management and land clearing operations
- Removal of excess biomass (fuel treatments) from timberlands and other forestlands
- Fuelwood extracted from forestlands
Secondary
- Primary wood processing mill residues
- Secondary wood processing mill residues
- Black liquor
Tertiary
- Urban wood residues — construction and demolition debris, tree trimmings, packaging wastes and consumer durables
In countries like India, human food demand for food and feed oilseed crops (e.g. soybean, sunflower) exceeds supply, so it is not desirable to divert large quantities of these crops for biodiesel. However large wasteland areas are available that might be cultivated with non-conventional oilseed species that are not eaten by humans but can withstand such rugged conditions, e.g. Pongamia and Jatropha. In recent years, juice from sweet sorghum (Sorghum bicolor) stalks is emerging as a viable source for bioethanol production. Sweet sorghum grows rapidly, is photosynthetically efficient due to its C4 metabolism, and is widely adaptable.
Cellulosic Biomass
Cellulosic ethanol technology is one of the most commonly discussed second-generation biofuel technologies worldwide. Cellulosic biofuels are derived from the cellulose in plants, some of which are being developed specifically as “energy” crops rather than for food production. These include perennial grasses and trees, such as switchgrass and Miscanthus. Crop residues, in the form of stems and leaves, represent another substantial source of cellulosic biomass.
To convert cellulose to ethanol, two key steps must occur. First, the cellulose and hemicellulose portions of the biomass must be broken down into sugars through a process called saccharification. The yielded sugars, however, are a complex mixture of five- and six-carbon sugars that provide a greater challenge for complete fermentation into ethanol. Second, these sugars must be fermented to make ethanol, as they are in grain-to-ethanol processes. The first step is a major challenge, and a variety of thermal, chemical and biological processes are being developed to carry out this saccharification step in an efficient and low-cost manner.
A number of research organisations and companies are exploring combinations of thermal, chemical and biological saccharification processes to develop the most efficient and economical route for the commercial production of cellulosic ethanol. These programmes have substantial government support, particularly in the United States and Canada. With the advent of new tools in the field of biotechnology, researchers have succeeded in producing several new strains of yeast and bacteria that exhibit varying degrees of ability to convert the full spectrum of available sugars to ethanol. However, the development of cellulosic ethanol technology has been hampered by technical problems associated with the separation of cellulose from lignin and the conversion of cellulose to sugars. Therefore, concentrating research on developing more efficient separation, extraction and conversion techniques is crucial to increase ethanol production.
Lignocellulosic Biomass
The largest potential feedstock for ethanol is lignocellulosic biomass, which includes materials such as agricultural residues (corn stover, crop straws, husks and bagasse), herbaceous crops (alfalfa, switchgrass), short rotation woody crops, forestry residues, waste paper and other wastes (municipal and industrial). Bioethanol production from these feedstocks could be an attractive alternative for disposal of these residues. Importantly, lignocellulosic feedstocks do not interfere with food security. Moreover, bioethanol is very important for both rural and urban areas in terms of energy security reason, environmental concern, employment opportunities, agricultural development, foreign exchange saving, socioeconomic issues etc.
The production of biofuels from ligno-cellulosic feedstocks can be achieved through two very different processing routes:
- Biochemical – in which enzymes and other micro-organisms are used to convert cellulose and hemicellulose components of the feedstocks to sugars prior to their fermentation to produce ethanol;
- Thermo-chemical – where pyrolysis/gasification technologies produce a synthesis gas (CO + H2) from which a wide range of long carbon chain biofuels, such as synthetic diesel or aviation fuel, can be reformed.
Lignocellulosic processing pilot plants have been established in the EU, in Denmark, Spain and Sweden. The world’s largest demonstration facility of lignocellulose ethanol (from wheat, barley straw and corn stover), with a capacity of 2.5 million litres, was established by Iogen Corporation in Ottawa, Canada. Many other processing facilities are now in operation or planning throughout the world.
Verenium, based in Cambridge (USA), has built a biorefinery to produce 1.4 million gallons of ethanol a year from cellulosic biomass, especially Bagasse, in Jennings, LA. The Verenium plant, operational since June 2008, is the first demonstration-scale cellulosic ethanol plant in the United States. The plant employs a combination of acid pretreatments, enzymes, and two types of bacteria to make ethanol from Bagasse. It will also process Energy Cane, a crop related to Sugarcane which is lower in Sugar and higher in fiber.
Algal Biomass
Among alternative feedstocks, algae holds enormous potential to provide a non-food, high-yield, non-arable land use source of biodiesel, ethanol and hydrogen fuels. Microalgae are the fastest growing photosynthesizing organism capable of completing an entire growing cycle every few days. Up to 50% of algae’s weight is comprised of oil, compared with, for example, oil palm which yields just about 20% of its weight in oil.
Algaculture (farming of algae) can be a route to making vegetable oils, biodiesel, bioethanol and other biofuels. Microalgae are one‐celled, photosynthetic microorganisms that are abundant in fresh water, brackish water, and marine environments everywhere on earth. The potential for commercial algae production is expected to come from growth in translucent tubes or containers called photo bioreactors or open ocean algae bloom harvesting. The other advantages of algal systems include:
- carbon capture from smokestacks to increase algae growth rates
- processing of algae biomass through gasification to create syngas
- growing carbohydrate rich algae strains for cellulosic ethanol
- using waste streams from municipalities as water sources
Algae have certain qualities that make the organism an attractive option for biodiesel production. Unlike corn-based biodiesel which competes with food crops for land resources, algae-based production methods, such as algae ponds or photobioreactors, would “complement, rather than compete” with other biomass-based fuels. Unlike corn or other biodiesel crops, algae do not require significant inputs of carbon intensive fertilizers. Some algae species can even grow in waters that contain a large amount of salt, which means that algae-based fuel production need not place a large burden on freshwater supplies.
Emerging Trends
A more recent process for converting complete biomass into a “biodiesel” is the BTL (biomass to liquid) technology. This uses gasification or pyrolysis (chemical decomposition of organic materials by heating in the absence of oxygen or any other reagents) to transform biomass into syngas (synthetic gas) and retransform it into diesel or gasoline. The development of BTL for the production of synthetic diesel is most advanced in Europe, particularly in Germany. Industry is expected to have its first industrial scale production plant operational within the next three to five years.
With new processes under development, it is now possible to reuse glycerol a by-product of the current biodiesel production process for biodiesel production. Biotransformation of glycerol into oils by means of algae and yeasts as well as the reintroduction of the residual glycerol in the biodiesel synthesis process means that 100% of the feedstock is used. This process should be commercially available within the next five years.
Challenges
Advanced biofuels provide promising opportunities which several companies have already embraced in order to invest for the future. These investments aim notably to reduce the relatively high production costs, to improve the efficiency of biomass to biofuels conversion and to reduce the costs of biomass transportation, by a better biomass logistics system.
Various technologies, which can optimize the use of crops or provide more efficient biomass pretreatment, are being investigated. Pretreatment of biomass is technically challenging and constitutes a large part of the processing cost. In the case of enzyme-based ligno-cellulosic ethanol for example, a package of enzymes/microbes will be required for hydrolysis (breakdown of cellulose to sugar) and fermentation; which adds significant process costs.
The commercialization of biofuels and advanced biofuels will also mean that infrastructure to harvest, transport, store and refine biomass must be developed. To avoid unnecessary transportation, biofuels and advanced biofuels production could be coupled with the production of other bio-based products in integrated biorefineries.
Conclusions
Fuels made from biomass provide unique environmental, economic strategic benefits and can be considered as a safe and clean liquid fuel alternative to fossil fuels. Significant progress has been made in the past several years in all aspects of cellulosic and lignocellulosic biomass conversion to ethanol. The areas of focus include low-cost thermochemical pretreatment, highly effective enzymes and efficient and robust fermentative microorganisms. Advances in pretreatment by acid catalyzed hemicellulose hydrolysis or employing an integrated approach in the form of consolidated bioprocessing with application of novel combination of enzymes for cellulose breakdown coupled with the recent development of genetically engineered microorganism are the major factors to make biofuel program successful at commercial scale.
Innovation in industrial biotechnology, especially in the development of enzymes that can convert hemicellulose and cellulose with improved efficiency, is vital to the development of advanced biofuels. The challenges from agricultural requirements to produce food and energy can only be met if we use all options available for increasing productivity and safeguarding harvests. Innovative crop protection products and plant biotechnology provide solutions to reduce the energy consumption in agriculture while conserving natural resources and contributing to mitigate the effect of climate change.
Salman Zafar is a Renewable Energy Advisor with rich experience in biomass energy, waste-to-energy processes, sustainable biofuels, solid waste management and renewable energy systems. He has been actively involved in promoting clean energy and sustainable waste management in different parts of the world. He is a prolific writer with many popular publications on topics related to renewable energy and waste management in reputed journals, magazines, newsletters, websites and blogs. Salman can be reached at salman.alg@gmail.com
The content & opinions in this article are the author’s and do not necessarily represent the views of AltEnergyMag
Comments (0)
This post does not have any comments. Be the first to leave a comment below.
Featured Product
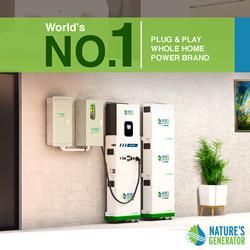
Nature's Generator MyGrid 10K
A 10,000W plug & play whole-home generator with a 10kWh LiFePO4 battery for reliable backup power. Features easy setup, flexible 120V/208-240V input, and solar/wind charging. Expandable with extra batteries or solar panels, and can pair two units for 20,000W for even larger energy needs. Powers your home during power outages, reduces electricity costs, and supports sustainable energy.