The ability to get PV costs down further will depend on bigger fabs and worker productivity.
Labor Costs Are Keeping PV Systems Expensive
David Gross | Silicon Equity Research LLC
The ability to get PV costs down further will depend on bigger fabs and worker productivity. |
![]() |
by David Gross, Senior Analyst,
Energy Technology Silicon Equity Research LLC |
With solar module prices slowly falling below $5 per watt, the PV industry has a renewed sense of optimism about matching the costs of traditional generation technologies. Venture capitalists are falling on top of themselves to fund new startups in this sector, and high oil prices have further encouraged governments across the globe to add funds to solar subsidy programs. However, as the industry attempts to wean itself off of government assistance, it is placing too much emphasis on materials, and ignoring simple labor issues that will persist regardless of what happens to silicon prices.
Since the advent of thin film modules in the early 90s, competing PV suppliers have been in a race to reduce the silicon content of their products. Yet even with silicon prices surging over $60 per kilo, materials still account for just 30% of the cost of goods sold for a typical panel. The balance is depreciation on furnaces and other fab equipment, and labor. Does Saving Materials Save Money? There is plenty of hype today about alternatives to traditional silicon panels. Wall Street is enamored with the stories of quantum dots and string ribbons creating the next generation of low cost systems. And while companies like Nanosolar and Evergreen Solar have interesting stories to tell, the cheapest modules on the market are made by Kyocera, whose 167 and 187 watt products retail for under $4 per watt excluding taxes and installation.. Kyocera's success battling costs didn't come from nanomaterials or thin films, but cheap labor. It serves the U.S. Market from a new facility in Tijuana. It reaches Germany, the largest solar market in Europe, from a plant in EU neighbor The Czech Republic. Evergreen Solar is in the process of building a European facility, but it has had to stay in high cost Germany due to a government rebate it will receive for locating there. While this assistance will reduce the company's capital requirements, it will not help it match Kyocera's operating cost advantage. Over eighty percent of Evergreen Solar's employees work in manufacturing, and unlike the semiconductor industry, there is no trend taking hold for module designers to go fabless. Without the equivalent of a Flextronics, TSMC, or Celestica to build panels, the PV industry has limited ability to reduce factory labor costs dramatically, because it is much harder for any one supplier to generate economies of scale when there are 20 other companies building similar facilities across the globe. Little Innovation with Installation While manufacturers can at least try to chip away at personnel costs in their factories, there is little they can do about labor costs associated with system installations. The industry has encouraged self-installation through marketing arrangements with Home Depot and Lowe's, but the vast majority of panels are still put into service by local resellers. Placing solar modules on rooftops typically costs $5,000 or more, and this is obviously not a cost that can be tackled by replacing crystalline silicon with quantum dots or some other high-tech substance. Factor in the battery and inverter, and the typical homeowner will spend about $10,000, or roughly $3 a watt, on peripheral products and services just to make his solar system functional. While battery and inverter costs have come down over time, and will likely continue to do so in the future, labor costs show no signs of dropping anytime soon. While the passage of Senate Bill 1 (the Million Roofs Initiative) in California is an encouraging development for the industry, the labor lobby in the Golden State is fighting to make union affiliation a requirement for PV installers. Subsidies Will Continue to Power Solar's Growth While there are plenty of vendor PowerPoints that suggest otherwise, the solar industry will continue to depend on subsidies, and will grow as a result of these government infusions, not because it can compete on a capital cost per watt basis with coal, natural gas, wind, hydro, or any other generation technology - AC, DC, or otherwise. In addition to the challenge of high labor costs, none of the exciting new production techniques allow manufacturing to occur any place less pure than a class 100,000 clean room, where it can cost hundreds of dollars per square foot just to filter the air. It is far more exciting to talk about nanomaterials and new technologies, which is why startups have jammed the press wires with exotic tales from their labs. However, the ability to get PV costs down further will depend on bigger fabs and worker productivity. |
|
The content & opinions in this article are the author’s and do not necessarily represent the views of AltEnergyMag
Comments (0)
This post does not have any comments. Be the first to leave a comment below.
Featured Product
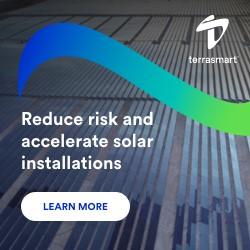