Simply put, HALT is superior to conventional testing because it is cost effective, faster, more accurate, compresses our product time to market, and maximizes customer satisfaction.
Xantrex Uses Halt To Enhance Product Reliability
Harry McLean | Xantrex
by
Harry McLean, Xantrex
All Xantrex power electronics products undergo significant testing before they are introduced to the market. In our quest to produce reliable, high-quality products, our engineers use accelerated reliability techniques to find product defects that may not be discovered using standard industry testing. We believe that by using advanced methods that go above and beyond conventional testing, we enhance product reliability, improve product quality, improve product time-to-market, and reduce product costs for our customers. This comprehensive testing is a unique competitive advantage that reinforces our position as a leader in the advanced power electronics industry.
An Overview
Our state-of-the-art chambers deliberately stress products and expose flaws that may not cause failures in regular use until long after a product is sold. Xantrex engineers test the robustness of each electronic design in a HALT chamber under extreme thermal and mechanical conditions. This rigorous testing allows us to identify and correct subtle design problems. It also helps us more accurately predict how, when and where product degradation may occur and its anticipated life span.
Why stress good hardware to such extremes? Our electronic products are used in a wide range of environments - from benign indoor settings such as homes and laboratories, to harsh outdoor areas where products are used in the engine compartment of a boat, mounted to the outside of a heavy duty truck, or installed on the side of a building where high winds and rapid temperature changes are common. Xantrex's reliability engineers will simulate these conditions in the accelerated test lab to ensure our product designs are rugged enough to continue operating effectively even after being exposed to these kinds of environmental stresses.
How the HALT works
The HALT chamber combines powerful thermal and vibration technologies to fatigue a product beyond product specifications. Following is a brief summary of how each procedure works.
Temperature
The temperature evaluation for our products is comprised of two processes: Cold and hot step stressing and rapid thermal transitions. Cold and hot stepping methods gradually introduce new temperatures to a product. For example, after a baseline diagnostic has been recorded on the product (e.g. 20°C, no vibration), the temperature is then lowered by 10°C, the product is tested under the new temperature, and the results are recorded. This process is repeated until the product begins to perform abnormally. Cold step stressing is performed first because it is less destructive than hot step stressing.
Rapid temperature changes are created by multiple high velocity fans inside the chamber, which produce temperatures ranging from lows of minus 100°C to highs of 200°C. Our products are subjected to the fastest temperature swings possible and their performance is closely monitored and evaluated. Both processes are helpful in detecting product thermal time to failure, thermal range and rate sensitivities.
Vibration
The
vibration stresses excite every part of a product, down to the component
structural level and far beyond what the product might see in its end use
environment. Pneumatic actuators capable of providing simultaneous repetitive
shock vibration stress our products across a wide frequency range. Our chamber
uses six degrees of freedom vibration versus a narrow spectrum of an x, y, z
axis vibration used in conventional methods. This multi-axis vibration testing
can be likened to turbulence one might experience on an airplane. It vibrates
the product in three orthogonal vectors and three rotational vectors
simultaneously and is useful in detecting potential product defects.
Combined Stresses
This step combines all of the previously used stresses. By combining temperature, temperature change, and multi-axis vibration, the combined accelerated tests expose design weaknesses beyond our product specifications so they can be corrected before the product is released into the market. Combined stress testing introduces a combination of environmental conditions that our products may experience in the field throughout their lifetime. It is the final and most rigorous test we conduct in HALT and it helps to ensure our products will operate reliably for our customers. Figure 2:
Fig.1 HALT failures induced by stress environment.
Benefits of accelerated testing
- Improves product reliability and robustness
- Allows us to detect and correct problems during the design phase
- Moves products into our customers' hands faster
- Reduces product costs for our customers
- Reduces warranty costs
- Decreases product failure in the field
- Allows us to stand behind our warranty with confidence
Traditional testing vs. accelerated testing
HALT is fundamentally different from conventional forms of testing because its purpose is to quickly find product weaknesses in an informed manner. The philosophy behind traditional methods is to test a product to set specifications, whereas HALT tests a product well beyond these specifications. Standard testing applies slower thermal changes, limited vibration and fewer stimuli; HALT testing exposes products to a wider vibration spectrum, extreme thermal rate changes, and multiple stimuli that are greater than what is expected in the end-use environment. This permits us to detect all potential failure modes, not just some.
HALT also accelerates a product's aging process from actual months into minutes. It takes from a few minutes, to a few days, compared to conventional testing, which takes weeks or longer. Simply put, HALT is superior to conventional testing because it is cost effective, faster, more accurate, compresses our product time to market, and maximizes customer satisfaction.
Xantrex stands by its name
When it comes to product reliability, Xantrex stands by its name. We understand that quality assurance is essential to success in today's competitive global market. We know that reliable products lead to happy customers. The benefits of HALT far outweigh standard industry testing and using HALT to test all our product designs reinforces our leadership and innovation in the power electronics industry.
About the author
Harry McLean is Xantrex's reliability engineering manager. Together with his team, he is responsible for assuring each product design undergoes a rigorous evaluation that includes HALT. He has more than 25 years experience in accelerated reliability techniques and has completed over 250 HALTs in industries including medical equipment, power electronics, avionics, telecommunications, automotive, printers, computers and storage devices.
The content & opinions in this article are the author’s and do not necessarily represent the views of AltEnergyMag
Comments (0)
This post does not have any comments. Be the first to leave a comment below.
Featured Product
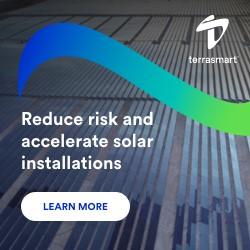